A well-designed warehouse is like a well-oiled machine, with each zone serving a specific purpose and contributing to smooth operations.
But did you know that a warehouse consists of 5 different zones?
In this article, we will dive into the intricacies of warehouse zoning and explore its five different zones.
Table of Contents
Toggle5 Zones of the Warehouse LISTED
Warehouse zoning is based on its functionality and purpose. As we said, each and every warehouse contains 5 key zones and these are:
- Receiving
- Storage
- Picking
- Packing
- Shipping
Each zone serves a specific purpose and has its own set of requirements and objectives.
By efficiently zoning a warehouse, businesses can optimize their operations, improve productivity, and enhance overall efficiency.
Zone 1: The Receiving Area
The receiving area is the first zone in a warehouse where items are received from suppliers or production facilities. This zone plays a crucial role in ensuring that raw materials or finished goods are accurately accounted for, inspected for quality, and prepared for further processing or storage.
When a shipment arrives at the receiving area, it undergoes a meticulous process to ensure that every item is accounted for and in optimal condition.
Skilled workers carefully unload the incoming shipments, cross-referencing the contents with purchase orders or packing lists to verify accuracy. This attention to detail is essential in preventing any discrepancies or errors that could lead to inventory discrepancies or delays in production. For businesses handling high order volumes, 3PL services in the USA can streamline the receiving and fulfillment process, ensuring efficient inventory management.
Key Functions of the Receiving Area
The receiving area performs several critical functions, including:
- Unloading incoming shipments and verifying their contents against purchase orders or packing lists.
- Checking the quality and condition of the received items to identify any damages or defects.
- Labeling and tagging items for proper identification and tracking.
- Updating inventory records to reflect the arrival of new stock.
Each of these functions requires a keen eye for detail and a commitment to accuracy. The quality control process in the receiving area ensures that any damaged or defective items are identified and addressed promptly, preventing them from entering the production or storage areas.
By carefully labeling and tagging items, the receiving area ensures that each item can be easily tracked throughout the warehouse, facilitating efficient inventory management.
Optimizing the Receiving Zone
To maximize efficiency in the receiving area, businesses can implement various strategies, such as:
- Designating specific receiving docks for different types of shipments to minimize congestion and streamline unloading processes.
- Using barcode scanners or RFID technology to automate data capture and reduce manual entry errors.
- Implementing cross-docking techniques to facilitate the direct transfer of goods from inbound to outbound shipments.
- Providing employees with adequate training and equipping them with the necessary tools and equipment to expedite receiving tasks.
Streamlining warehouse receiving processes is crucial for efficient inventory management. Fulfyld’s 3PL warehouse services ensure seamless receiving, storage, and distribution.
By designating specific receiving docks for different types of shipments, businesses can optimize the flow of goods and minimize the time spent on unloading. This strategic approach reduces congestion and ensures that each type of shipment is efficiently handled.
Additionally, the implementation of barcode scanners or RFID technology automates the data capture process, reducing the risk of manual entry errors and expediting the verification and tracking of received items.
Cross-docking techniques further enhance efficiency in the receiving area. By facilitating the direct transfer of goods from inbound to outbound shipments, businesses can eliminate the need for intermediate storage, reducing handling costs and streamlining the supply chain process.
Lastly, providing employees with adequate training and equipping them with the necessary tools and equipment is crucial for expediting receiving tasks. Well-trained staff can efficiently handle the unloading, inspection, and documentation processes, ensuring that the receiving area operates smoothly and effectively.
Zone 2: The Put-Away Zone
The put-away zone is where goods are stored after being received and inspected. This zone plays a crucial role in maintaining inventory accuracy and accessibility. But what exactly happens in this zone? Let’s dive deeper into the role and strategies for efficient put-away operations.
Role of the Put-Away Zone
The primary function of the put-away zone is to ensure that items are stored in their designated locations in a systematic manner, allowing for easy retrieval when needed. This not only saves time but also reduces the risk of misplaced or lost items. Key activities within this zone include:
- Assigning storage locations based on factors such as item dimensions, weight, and demand frequency. This meticulous planning ensures that items are stored in the most optimal locations, maximizing the use of available space.
- Organizing items in a way that maximizes available space and minimizes the need for excessive movement or rearrangement. By utilizing efficient storage techniques such as stacking or using specialized racks, businesses can make the most of their storage capacity.
- Updating inventory records to reflect changes in item location and quantity. Accurate and up-to-date inventory records are essential for efficient operations and preventing stockouts or overstock situations.
- Implementing inventory control measures such as cycle counting or random spot checks to ensure ongoing accuracy. Regular audits help identify any discrepancies between physical stock and recorded quantities, allowing for timely corrections.
Strategies for Efficient Put-Away Operations
Efficient put-away operations require careful planning and execution. Here are some strategies that can help businesses optimize their put-away zone:
- Implementing an automated storage and retrieval system (AS/RS) to minimize human intervention and expedite put-away processes. These systems use advanced technologies like robotics or conveyors to transport and store items, reducing the chances of errors and increasing efficiency.
- Using color-coded labels or signage to clearly indicate storage locations and enable easy visual identification. This simple yet effective technique helps employees quickly locate the right storage spot, reducing search time and minimizing errors.
- Employing slotting techniques that prioritize fast-moving or high-demand items to reduce picking and replenishment time. By strategically placing frequently accessed items closer to the pick-up area, businesses can streamline their operations and improve order fulfillment speed.
- Providing training to employees to ensure they understand the importance of proper put-away procedures and adhere to best practices. Well-trained staff can contribute significantly to maintaining accuracy and efficiency in the put-away zone.
By implementing these strategies and emphasizing the importance of the put-away zone, businesses can optimize their inventory management processes, reduce costs, and improve customer satisfaction.
The put-away zone may be the second zone in the warehouse, but its impact on overall operations should never be underestimated.
Zone 3: The Storage Area
The storage area is where items are kept until they are needed for order fulfillment or other purposes. This zone requires careful planning to optimize space utilization and ensure efficient retrieval of goods.
Understanding the Storage Area’s Purpose
The storage area serves as a repository for goods that are not immediately required, providing a physical buffer between the receiving and picking zones. Its key objectives include:
- Maximizing available space by utilizing vertical storage solutions such as high-reach forklifts or automated retrieval systems.
- Organizing stored items in a logical and systematic manner to facilitate easy access and minimize search time.
- Implementing proper inventory labeling and documentation to accurately track item location and quantity.
- Regularly conducting stock audits and checks to verify inventory accuracy and identify any discrepancies.
Maximizing Space in the Storage Zone
To optimize space utilization in the storage area, businesses can consider the following strategies:
- Implementing a bin location system that assigns unique identifiers to specific storage locations, enabling efficient item tracking and retrieval.
- Utilizing racking systems such as selective pallet racks, drive-in racks, or push-back racks to maximize vertical space and accommodate different types of items.
- Implementing a first-in, first-out (FIFO) or last-in, first-out (LIFO) inventory rotation policy based on the specific storage requirements of the goods.
- Regularly reviewing inventory turnover rates and making necessary adjustments to minimize storage costs and prevent obsolescence.
Efficient warehouse management depends on optimizing inventory space and storage solutions. Read our guide on how to create a free barcode inventory system in Excel.
Zone 4: The Picking Area
The picking area is where items are retrieved from storage based on order requirements. This zone is critical for order fulfillment and plays a significant role in meeting customer expectations.
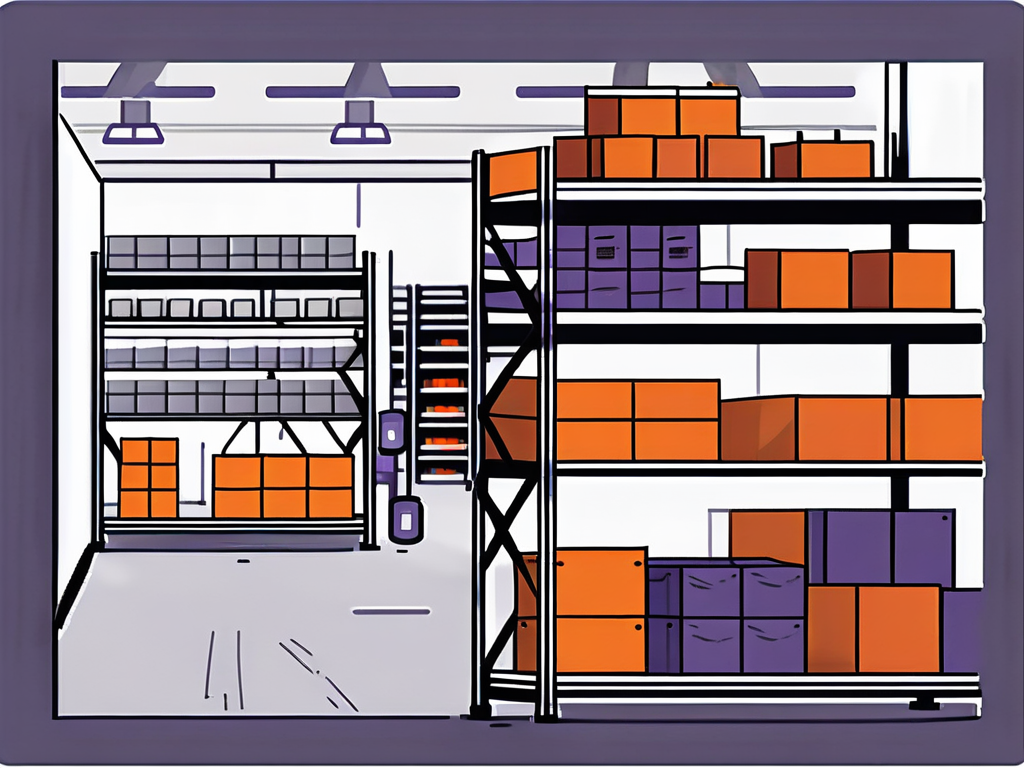
The Picking Area’s Role in Warehouse Operations
The primary objective of the picking area is to ensure accurate and efficient retrieval of items for order fulfillment. Key functions within this zone include:
- Receiving picking instructions and selecting items from their designated storage locations.
- Packing the picked items in appropriate containers or cartons while ensuring proper handling and protection.
- Updating the inventory system to reflect the quantity of items picked and processed for shipment.
- Routing the picked items to the appropriate staging area for further processing or direct shipment.
Enhancing Efficiency in the Picking Zone
To improve picking operations and enhance overall efficiency, businesses can implement the following strategies:
- Using warehouse management systems (WMS) or order-picking technologies such as voice-guided or barcode scanning devices to reduce errors and expedite picking tasks.
- Implementing batch picking or zone picking approaches to consolidate multiple orders or optimize travel routes within the picking area.
- Providing clear instructions, signage, or labeling to guide pickers and facilitate accurate and timely item selection.
- Regularly analyzing picking data, such as pick rates and error rates, to identify areas for improvement and implement appropriate training or process enhancements.
A well-structured pick and pack fulfillment strategy can significantly improve warehouse productivity and order accuracy. Learn more about Fulfyld’s pick and pack services.
Zone 5: The Shipping Area
The shipping area in a warehouse plays a critical role as the final checkpoint before products reach customers, making it a pivotal zone for ensuring customer satisfaction and operational efficiency. This area is where all the prepared orders come together, ready to be dispatched to their final destinations. The efficiency and organization of the shipping area directly impact delivery speed, accuracy, and the overall quality of the delivery experience, which are key drivers of customer satisfaction.
In the shipping area, several key activities take place, including the final inspection of orders for accuracy, securing packages to prevent damage during transit, and sorting shipments based on their destinations. The layout and management of this zone are designed to streamline processes, reducing bottlenecks and errors that could delay deliveries.
To enhance functionality and efficiency, the shipping area includes several essential elements:
- Staging Zones: Dedicated spaces where orders are organized based on their shipping priority and destination.
- Loading Docks: Areas equipped for loading orders onto transportation vehicles efficiently, often with adjustable platforms to accommodate different vehicle sizes.
- Labeling Stations: Stations where orders are labeled with shipping information, including destination, tracking numbers, and handling instructions.
- Quality Control Points: Spots designated for the final inspection of orders, ensuring that packages are secure and correctly labeled before dispatch.
- Carrier Coordination Center: A hub for coordinating with shipping carriers, scheduling pickups, and managing logistics documentation.
By focusing on optimizing these components, warehouses can ensure that the shipping area operates smoothly, facilitating timely deliveries and maintaining high levels of customer satisfaction. The strategic organization of the shipping area not only enhances operational efficiency but also plays a significant role in the overall success of the warehouse’s logistical capabilities.
The Importance of Warehouse Zoning
Warehouse zoning plays a crucial role in ensuring streamlined workflow and reducing unnecessary movement and downtime. By clearly defining areas for each task, employees can navigate the warehouse more efficiently, saving time and effort.
Additionally, proper zoning improves inventory management and reduces the risk of errors, leading to enhanced customer satisfaction and profitability.
Effective SKU management is essential for optimizing warehouse zoning and stock organization. Learn about the best practices for effective SKU rationalization.
Principles of Warehouse Zoning
Effective warehouse zoning is based on several key principles that align with the specific requirements of a business. These principles include:
- Resource Optimization: Ensuring that resources such as space, equipment, and labor are allocated optimally.
- Accessibility: Creating clear pathways and easy access to different zones for smooth movement of goods and personnel.
- Seamless Workflow: Designing zones in a way that minimizes bottlenecks and allows for a continuous flow of operations.
- Flexibility: Building zoning structures that can be easily adapted or modified to accommodate changes in demand or organizational needs.
Resource optimization is a critical aspect of warehouse zoning. By carefully analyzing the available space, businesses can determine the most efficient use of their resources.
This includes strategically placing equipment and organizing inventory to minimize wasted space and maximize productivity. Additionally, optimizing labor allocation ensures that employees are assigned tasks that align with their skills and expertise, further enhancing efficiency.
Accessibility is another key principle of warehouse zoning. Creating clear pathways and easy access to different zones allows for smooth movement of goods and personnel.
This not only reduces the risk of accidents and injuries but also enables employees to quickly locate and retrieve items, improving overall productivity. By implementing proper signage and labeling systems, businesses can further enhance accessibility and ensure that employees can easily navigate the warehouse.
Optimize Warehouse Flow and Productivity Through Strategic Zoning
In the world of warehousing, effective zoning is the secret ingredient for operational success. Each of the five zones—receiving, put-away, storage, picking—plays a vital role in ensuring a smooth workflow, minimizing errors, and maximizing efficiency.
By understanding the purpose and implementing the right strategies within each zone, businesses can optimize their warehouse operations and gain a competitive edge in today’s fast-paced business environment. For expert fulfillment and logistics solutions, Fulfyld offers tailored warehouse management services to help streamline operations and improve efficiency.