Did you know that accurate replenishment cycle calculation is crucial for effective inventory management? Being able to determine when and how much inventory to order can save businesses time, money, and headaches.
In this article, we will explore the ins and outs of calculating the replenishment cycle and provide you with a step-by-step guide to help you optimize your inventory management process.
Stay with us and learn:
- Basics of replenishment cycles and their components
- How to gather essential data for calculating replenishment cycles
- Key factors influencing the replenishment cycle, including supplier reliability and seasonal demand
- Strategies to optimize your replenishment cycle for better inventory management
Table of Contents
Toggle3 Easy-to-Follow Steps for Calculating Replenishment Cycle
Now that we understand the components of the replenishment cycle, let’s walk through the step-by-step process of calculating it. Efficient inventory management is essential for seamless fulfillment, and businesses utilizing 3PL services in the USA can optimize their replenishment process to prevent stockouts and reduce excess inventory.
Step 1: Gather Necessary Data
The first step in calculating the replenishment cycle is gathering the necessary data. This includes information such as:
- Historical sales data
- Lead time
- Demand forecast
- Safety stock level
Having accurate and up-to-date data is essential for making informed decisions.
Historical sales data provides insights into past trends and patterns, helping you anticipate future demand. Lead time refers to the duration between placing an order and receiving it, influencing how much safety stock you need to hold.
Demand forecast estimates the quantity of a product that customers will purchase over a specific period, guiding your replenishment decisions. Safety stock acts as a buffer against unexpected demand spikes or supply chain disruptions, ensuring continuity in operations.
Step 2: Apply the Replenishment Cycle Formula
Once you have gathered the necessary data, you can now apply the replenishment cycle formula. There are various formulas and methods available, depending on the specific needs of your business. It is essential to choose the formula that best suits your requirements and ensures a reliable calculation of the replenishment cycle.

Common replenishment cycle formulas include Economic Order Quantity (EOQ), Reorder Point (ROP), and Just-in-Time (JIT) inventory systems. EOQ helps determine the optimal order quantity to minimize total inventory costs. ROP sets a threshold at which new orders should be placed to avoid stockouts. JIT aims to reduce inventory holding costs by ordering only when needed, aligning supply with demand efficiently.
Step 3: Calculate Replenishment Cycle
Once you have gathered the necessary data and chosen the appropriate formula, you can proceed with calculating the replenishment cycle. Here’s how:
Determine Lead Time Demand
Calculate the total demand during the lead time. This involves multiplying the average daily demand by the lead time in days.
For example, if your average daily demand is 50 units and your lead time is 10 days, the lead time demand is 50 * 10 = 500 units.
Calculate Safety Stock
Safety stock is an additional quantity of inventory kept to mitigate risks of stockouts due to uncertainties in demand or supply.
The formula for safety stock varies, but a common approach is to use the standard deviation of lead time demand and a desired service level (e.g., 95% service level).
For instance, if the standard deviation of lead time demand is 20 units and you aim for a 95% service level (z-score of 1.65), the safety stock would be 1.65 * 20 = 33 units.
Determine Reorder Point
The reorder point (ROP) is the inventory level at which a new order should be placed to replenish stock before it runs out.
The formula for ROP is: ROP = Lead Time Demand + Safety Stock.
Using the previous examples, if the lead time demand is 500 units and safety stock is 33 units, the ROP would be 500 + 33 = 533 units.
Calculate Economic Order Quantity (EOQ)
EOQ helps determine the optimal order quantity that minimizes total inventory costs.
The formula for EOQ is: EOQ = √((2DS) / H), where D is annual demand, S is the order cost per order, and H is the holding cost per unit per year.
For example, if annual demand (D) is 10,000 units, order cost (S) is $100, and holding cost (H) is $2 per unit, EOQ would be √((2 * 10,000 * 100) / 2) = 316 units.
Basics of Replenishment Cycle
Before we dive into the nitty-gritty details, let’s first establish what exactly a replenishment cycle is. Put simply, the replenishment cycle is the period of time it takes to reorder and restock inventory after it has been depleted. It involves several key components that work together to ensure a smooth flow of goods from suppliers to customers.
When delving deeper into the concept of a replenishment cycle, it becomes evident that this process is not just about restocking shelves. It encompasses a strategic approach to managing inventory levels, supplier relationships, and customer demand. By understanding the intricacies of the replenishment cycle, businesses can streamline their operations and enhance overall efficiency.
Components of the Replenishment Cycle
The replenishment cycle comprises several key components that need to be taken into consideration during the calculation process. Let’s take a closer look at these components:
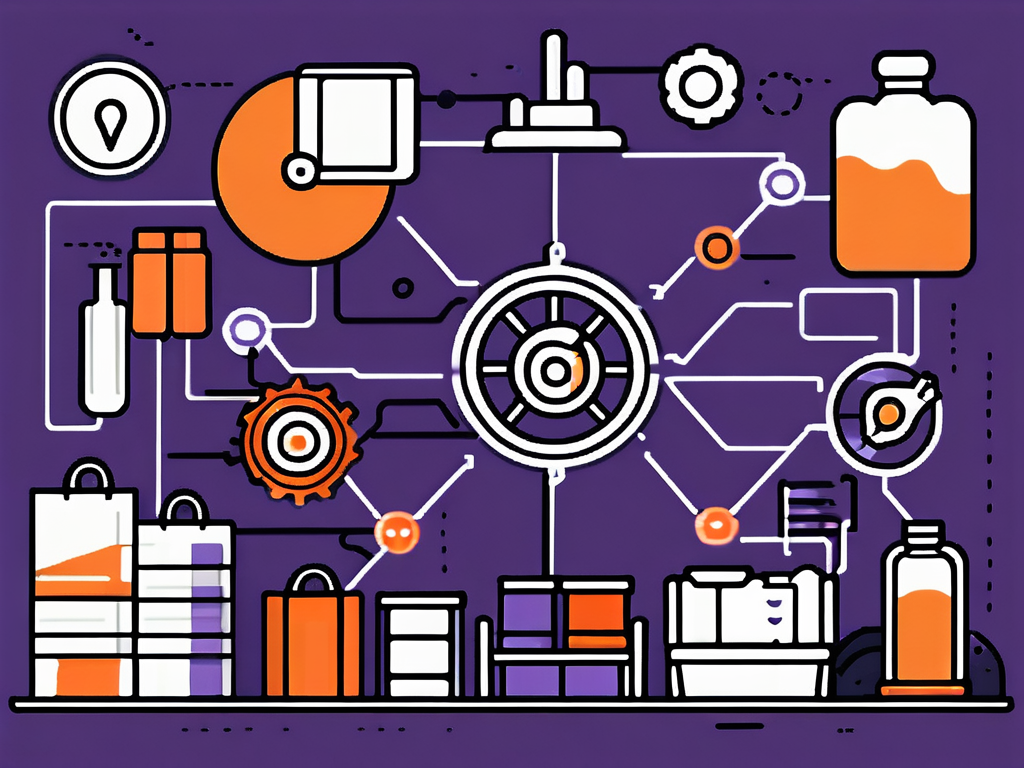
Lead Time
Lead time refers to the time it takes for an order to be processed, shipped, and delivered to your business. This includes the time it takes for your supplier to receive and process your order, as well as the time it takes for the goods to be transported to your location. Understanding the lead time is crucial for accurately predicting when you should place your order to ensure timely replenishment.
Lead time can vary depending on various factors such as:
- The location of the supplier
- Shipping methods
- Any potential delays in the supply chain
It is essential for businesses to have a clear understanding of lead time to avoid stockouts and maintain a smooth replenishment process.
Demand During Lead Time
During the lead time, your business will continue to receive customer orders and experience demand for the product. It is important to factor in this demand when calculating the replenishment cycle to ensure that you have enough stock to meet customer needs during the lead time.
Forecasting demand accurately during the lead time is crucial for businesses to prevent stockouts or overstock situations. By analyzing historical data and market trends, businesses can better anticipate customer demand and adjust their replenishment cycle accordingly.
Safety Stock
Safety stock is an additional level of inventory that businesses keep on hand to safeguard against unexpected fluctuations in demand or disruptions in the supply chain. Calculating the appropriate amount of safety stock is crucial for maintaining operational efficiency and customer satisfaction.
Factors such as seasonality, market trends, and supplier reliability can impact the need for safety stock. By conducting thorough risk assessments and considering external factors, businesses can determine the optimal level of safety stock to mitigate potential disruptions and ensure continuous supply chain operations.
Factors Influencing the Replenishment Cycle
When calculating the replenishment cycle, it is important to consider various factors that can influence its duration. Let’s explore some of the key factors:
Factor 1: Supplier Reliability
The reliability of your suppliers plays a crucial role in the replenishment cycle. If your suppliers consistently deliver goods on time and as promised, it can help streamline the replenishment process and minimize disruptions.
Building strong relationships with suppliers through effective communication and collaboration can also enhance reliability. Regularly reviewing supplier performance metrics and providing feedback can further strengthen the partnership, leading to smoother replenishment cycles.
Factor 2: Seasonal Demand Fluctuations
Many businesses experience seasonal variations in customer demand. It is important to take these fluctuations into account when calculating the replenishment cycle to ensure that you have enough stock to meet peak demands during specific periods.
Utilizing historical sales data and market trends can help predict seasonal demand patterns more accurately. By analyzing past sales performance and customer behavior, businesses can adjust their replenishment strategies to align with anticipated demand fluctuations.
Factor 3: Inventory Management Policies
Your inventory management policies and strategies can have a significant impact on the replenishment cycle. Implementing efficient inventory control systems, ensuring accurate demand forecasting, and optimizing safety stock levels are all important factors to consider.
Utilizing technology such as inventory management software can streamline the tracking of stock levels and automate replenishment processes. By leveraging data analytics and real-time inventory monitoring, businesses can make informed decisions to improve the efficiency of their replenishment cycles and overall inventory management practices.
Strategies for Optimizing Replenishment Cycle
Now that we have covered the basics of replenishment cycle calculation, let’s explore some strategies you can implement to optimize it:
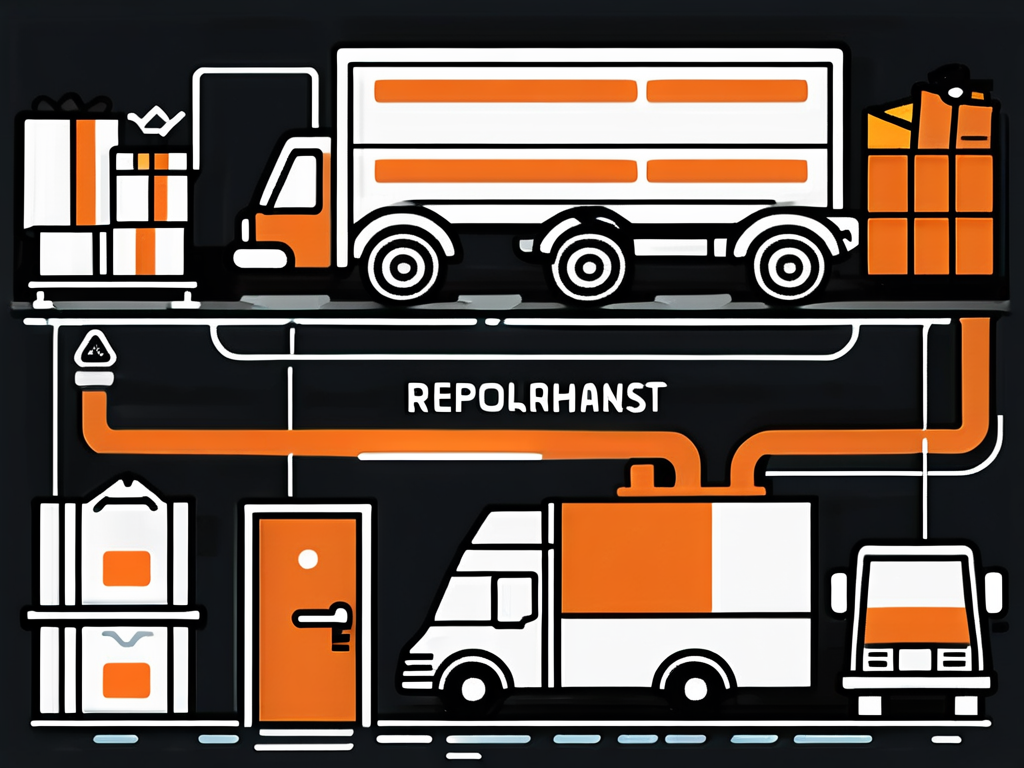
Improving Supplier Relationships
By establishing strong relationships with your suppliers, you can improve communication, reliability, and turnaround times. This can help you streamline the replenishment process and reduce lead times.
One way to improve supplier relationships is to schedule regular meetings with them to discuss your inventory needs and any upcoming promotions or events that may impact demand. This open line of communication allows your suppliers to better understand your business and enables them to plan their production and delivery schedules accordingly.
Additionally, consider implementing a vendor-managed inventory (VMI) system. With VMI, your suppliers take on the responsibility of monitoring your inventory levels and initiating replenishment orders when necessary. This not only reduces the burden on your team but also ensures that stock is replenished in a timely manner, minimizing the risk of stockouts.
Implementing Advanced Forecasting Techniques
Utilizing advanced forecasting techniques, such as data analytics and predictive modeling, can help you accurately predict future demand. This will enable you to adjust your replenishment cycle accordingly, ensuring that you have the right amount of stock at the right time.
One powerful tool for forecasting is demand sensing, which uses real-time data from various sources, including point-of-sale systems, social media, and weather patterns, to predict customer demand. By analyzing this data, you can identify trends, seasonality, and even unexpected shifts in demand, allowing you to make more informed decisions about your replenishment cycle.
Adjusting Safety Stock Levels
Regularly reviewing and adjusting safety stock levels based on demand fluctuations and changes in market conditions can help you optimize your replenishment cycle. By having the appropriate amount of safety stock, you can minimize the risk of stockouts and maintain a steady supply of inventory.
Optimize Your Inventory with Accurate Replenishment Cycle Calculation
Calculating the replenishment cycle is a critical aspect of effective inventory management. By understanding the basics, considering the various components and factors, and implementing optimization strategies, businesses can ensure a smooth flow of goods, maximize profitability, and keep customers satisfied. Partnering with Fulfyld for 3PL fulfillment services can further streamline inventory management, helping businesses maintain optimal stock levels and reduce fulfillment delays.
So, take the time to crunch the numbers, improve supplier relationships, implement advanced forecasting techniques, and adjust safety stock levels to optimize your replenishment cycle today!