Choosing the best inventory costing method is crucial for accurately valuing inventory, determining the cost of goods sold, and ultimately, reflecting the true financial health of your business. The right method can influence your profitability, tax liabilities, and decision-making processes.
Each method has its advantages and disadvantages, but, it’s essential to understand which one is the most suitable inventory costing method for your business. In this article we will discuss:
- Top inventory costing method
- Different inventory costing methods and how to choose the right method for your needs
- Why is inventory costing important
Table of Contents
ToggleBest Inventory Costing Strategies for Your Business
The best inventory costing methoddepends on the specific needs and circumstances of your business. Generally, First-In, First-Out (FIFO) is preferred during periods of rising prices because it matches older, lower-cost inventory with current revenues, resulting in higher profits and lower tax liabilities.
Last-In, First-Out (LIFO) is beneficial for reducing tax liabilities in inflationary times as it matches higher-cost inventory with current revenues, reducing reported profits.
The Weighted Average Cost method smooths out price fluctuations and is useful for businesses with consistent inventory turnover. Each method has its advantages and choosing the right one depends on factors such as:
- Inventory turnover rate
- Tax implications
- Financial reporting preferences
Different Types of Inventory Costing Methods
Now, let’s explore some common inventory costing methods. Each method has its advantages and disadvantages, so it’s crucial to choose one that aligns with your business model and objectives.
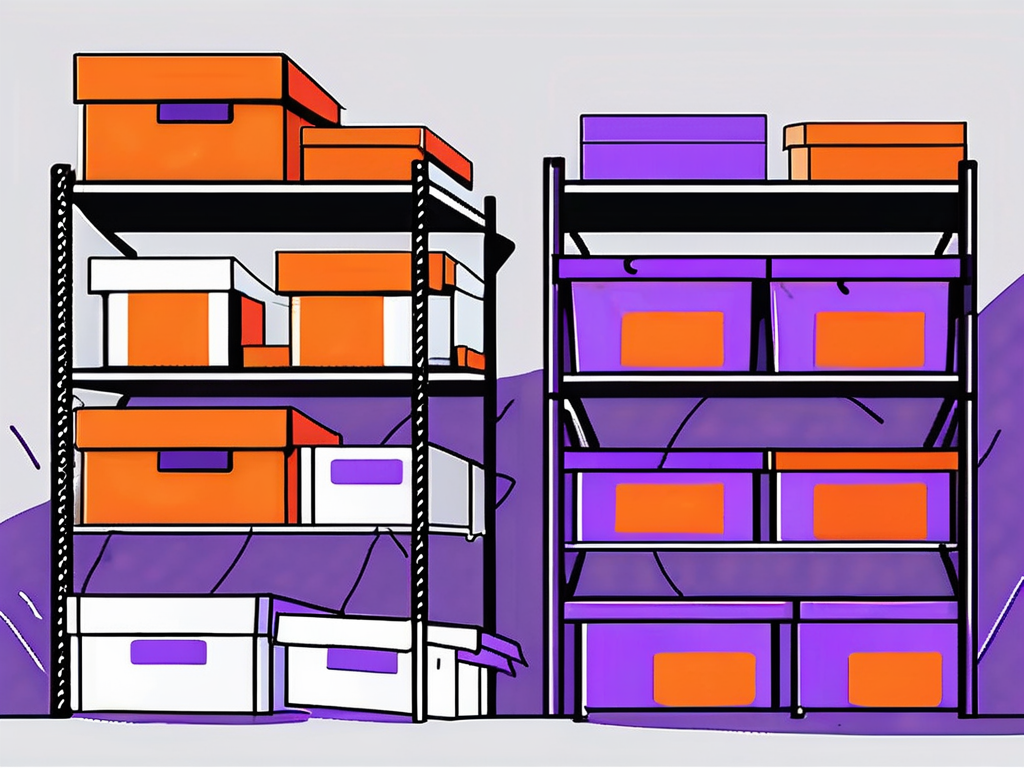
First-In, First-Out (FIFO)
The FIFO method assumes that the first inventory items purchased or produced are the first ones sold. It matches the latest costs to the ending inventory, resulting in a more accurate representation of current costs. This method is suitable for businesses dealing with perishable or time-sensitive products.
For example, a bakery that produces fresh bread daily would benefit from using the FIFO method. By assuming that the first bread baked is the first one sold, the bakery can ensure that the inventory value reflects the most recent costs, accounting for any changes in ingredient prices or production costs.
Last-In, First-Out (LIFO)
The LIFO method assumes that the most recently purchased or produced items are the first ones sold. This approach can be beneficial during periods of inflation as it allocates higher costs to the goods sold, reducing taxable income. However, it may not reflect the actual market value of the inventory.
Imagine a car dealership that uses the LIFO method. During times of inflation, when the prices of cars are rising, the dealership can benefit from reporting lower taxable income by assigning the higher costs to the cars sold. However, it’s important to note that this method may not accurately represent the current market value of the remaining inventory, which could impact decision-making regarding pricing and profitability analysis.
Weighted Average Cost
In this method, the average cost of all inventory items is calculated periodically. It divides the total cost of goods available for sale by the total units available, providing a per-unit average cost. This approach smoothes out fluctuations in costs and is commonly used in industries where prices change frequently.
For instance, a retail clothing store that frequently restocks its inventory with new fashion items may find the weighted average cost method beneficial. By calculating the average cost of all inventory items, the store can maintain stable pricing and avoid sudden price fluctuations that could negatively impact customer satisfaction and sales.
Specific Identification
Under the specific identification method, each individual unit of inventory is assigned a specific cost. This method is suitable for businesses that deal with unique or high-value items, such as jewelry or artwork. While it offers the most accurate cost allocation, it can be impractical for large quantities of inventory.
Consider a high-end jewelry store that deals with unique and valuable pieces. By using the specific identification method, the store can accurately allocate costs to each individual piece of jewelry, considering factors like:
- Gemstone quality
- Craftsmanship
- Design intricacies
This ensures that the inventory value reflects the true value of each item, enabling the store to make informed pricing decisions and maintain profitability.
How to Choose the Best Inventory Costing Method
Choosing the best inventory costing method requires careful evaluation and consideration of various factors. Let’s explore some essential aspects to help guide your decision-making process.
Factors to Consider
Consider factors such as:
- Nature of your business
- Type of inventory you deal with
- Availability of historical cost data
Pay attention to any regulations or industry-specific guidelines that may dictate the use of certain costing methods.
Furthermore, assessing the reliability of cost data is paramount. Inaccurate or outdated cost information can skew your financial reports and lead to misinformed business decisions. Implementing a robust system for tracking and updating cost data can enhance the accuracy of your inventory costing method.
Impact on Financial Statements
Each inventory costing method affects financial statements differently. For accurate bookkeeping and financial analysis, it’s essential to understand how each method impacts metrics such as:
- COGS
- Gross profit
- Net income
Moreover, consider the implications of inventory valuation methods on your balance sheet. The choice of costing method can influence the reported value of inventory on your financial statements, which in turn can impact metrics like working capital and inventory turnover ratio. Striking a balance between accurate financial reporting and tax efficiency is key.
Tax Implications
Inventory costing methods can have significant tax implications. For example, the LIFO method, which assigns higher costs to inventory, may result in lower taxable income and reduced tax liabilities. Consult with a tax professional to determine which method is most advantageous in terms of tax planning.
Additionally, consider the long-term implications of your chosen inventory costing method. Changes in costing methods can have ripple effects on financial performance and tax obligations over multiple accounting periods. Conducting scenario analyses and sensitivity testing can help you anticipate the potential outcomes of different costing methods under varying market conditions.
Implementing Your Chosen Inventory Costing Method
Once you have decided on the best inventory costing method for your business, you’ll need to implement it effectively. Here are two crucial steps:
Transitioning to a New Costing Method
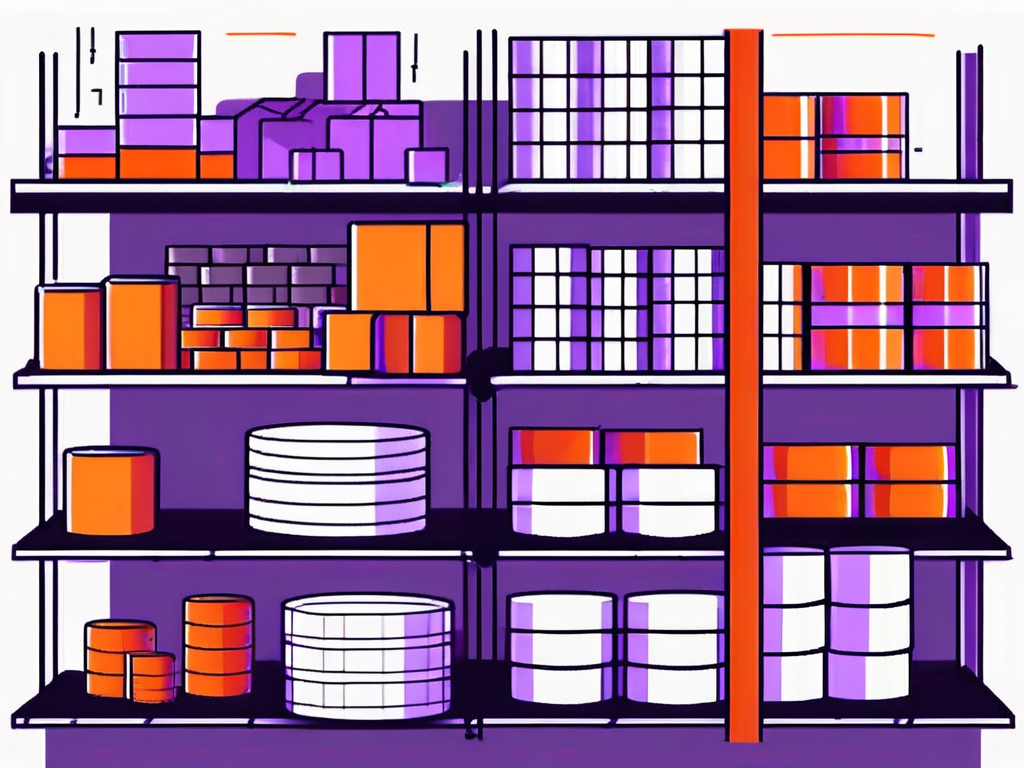
Switching to a new costing method requires careful planning and consideration. Ensure you have accurate historical cost data and develop a clear transition plan to minimize disruptions to your operations. Communicate the changes to your team and provide training if necessary to ensure a smooth transition.
Maintaining Consistency in Costing
To ensure the accuracy and reliability of your financial statements, it’s vital to maintain consistency in your chosen costing method. Deviating from the method can lead to inconsistencies and hinder accurate performance comparisons over time. Regularly review your costing practices to ensure that they continue to align with your business needs.
Remember, the best inventory costing method for your business depends on several factors unique to your operations. By understanding the concepts and evaluating the options, you can select the right method to guide your financial success. So, choose wisely and let the magic of accurate inventory costing lead you to financial prosperity!
When transitioning to a new costing method, it’s essential to involve key stakeholders in the decision-making process. Seek input from various departments within your organization to ensure that the chosen method aligns with the overall business strategy. By fostering collaboration and transparency, you can gain valuable insights and buy-in from those who will be directly impacted by the change.
Utilizing Technology for Costing Efficiency
Technology plays a crucial role in modern inventory costing practices. Consider implementing inventory management software that integrates seamlessly with your chosen costing method. These tools can:
- Automate calculations
- Track inventory levels in real-time
- Generate detailed reports
Embracing technology can streamline your costing processes and improve overall efficiency.
The Importance of Inventory Costing
Proper inventory costing provides businesses with accurate insights into their:
- Cost of goods sold
- Gross profit
- Overall financial health
It enables managers to make informed decisions about pricing, purchasing, and production. By understanding the true costs of inventory, companies can optimize their operations, giving them a competitive edge in the market.
Key Terms in Inventory Costing
Now, let’s familiarize ourselves with some essential terminology:
- Cost of Goods Sold (COGS): This is the total cost incurred by a company to produce or purchase the goods it sells. COGS includes direct costs such as materials, labor, and overhead expenses directly associated with production.
- Gross Profit: It represents the difference between net sales revenue and the cost of goods sold. Gross profit is a measure of profitability before deducting operating expenses. It provides insights into a company’s ability to generate revenue from its core operations.
- Ending Inventory: The value of unsold goods at the end of an accounting period. It is crucial for accurate financial statements and plays a significant role in determining a company’s profitability and financial position.
Understanding these key terms is like deciphering the language of inventory costing. They form the foundation upon which businesses build their financial strategies, ensuring accurate reporting and informed decision-making.
Choose the Right Inventory Costing Method for Success
Selecting the appropriate inventory costing method is essential for accurately valuing inventory, determining cost of goods sold, and making informed financial decisions. The right method can significantly impact your profitability, tax liabilities, and overall financial health.
Understanding and implementing the most suitable inventory costing strategy for your business ensures precise financial reporting and optimal operational efficiency, and incorporating Fulfyld can further enhance your operational effectiveness.