FIFO Method Calculator: Optimize Stock Rotation and Minimize Waste
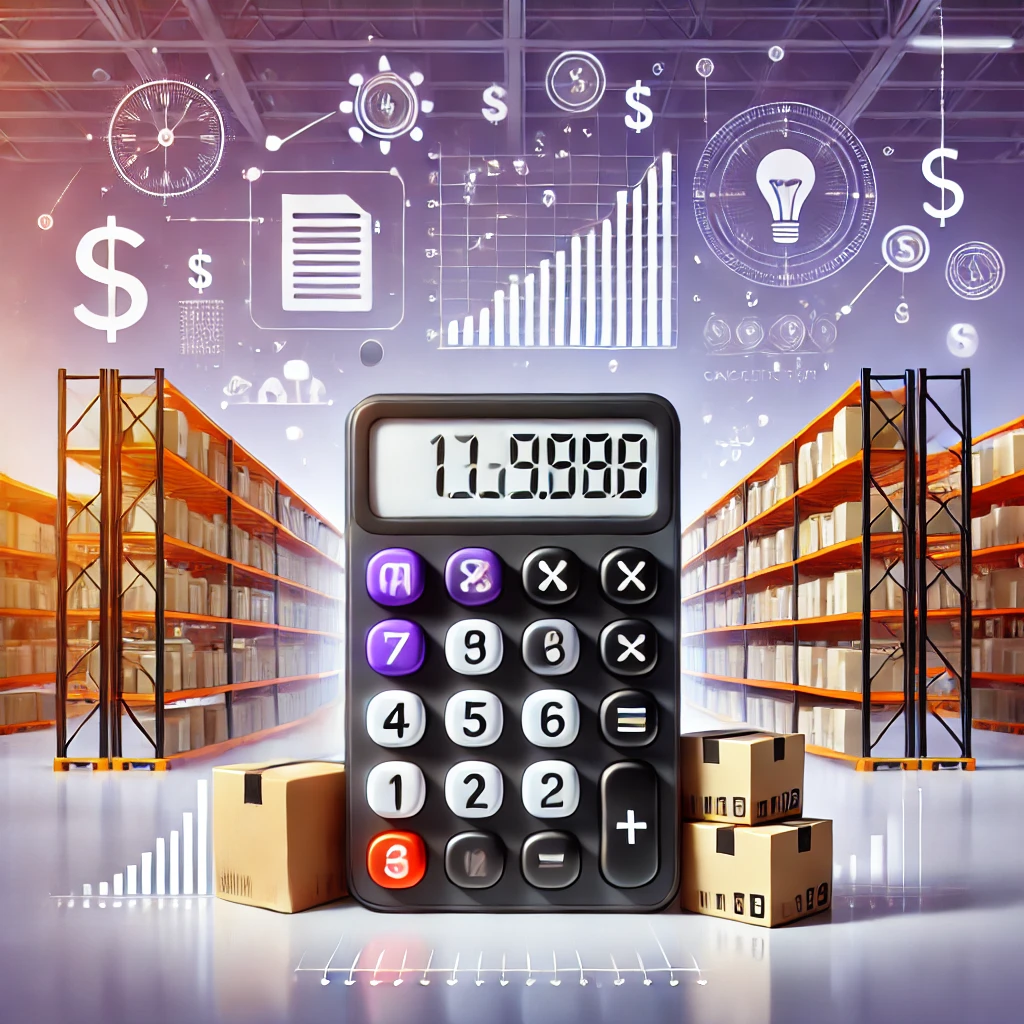
Efficient inventory management is key to sound financial planning, and our FIFO Method Calculator makes it simpler than ever. Using the First-In, First-Out method, this tool provides precise calculations for inventory costs, ensuring your oldest stock is accounted for first.
Ideal for businesses of any scale, the calculator helps you determine the Cost of Goods Sold (COGS) and ending inventory values quickly and accurately, giving you a clear picture of your financial performance.
Take charge of your inventory valuation today and make smarter decisions for your business with this reliable and intuitive tool!
FIFO Inventory Calculator
Results:
FIFO Calculator: A Component-by-Component Guide for Fresh Stock Management
The First-In, First-Out (FIFO) method prioritizes selling or using your oldest inventory first – think of it like a grocery store’s dairy case where the oldest milk is placed at the front. Let’s explore how each component of our calculator helps you manage this natural flow of inventory.
1. The Purchase Timeline
Your inventory story begins with the Purchase Entry section – the backbone of FIFO calculations.
Key Aspects:
- Each entry represents a chapter in your inventory timeline
- Earlier entries get priority in cost calculations
- Perfect for industries where age matters (food, pharmaceuticals, technology)
Real-World Application: A bakery receives three flour deliveries:
- First Delivery: 100 bags at $15/bag
- Second Delivery: 150 bags at $16/bag
- Third Delivery: 200 bags at $17/bag
Under FIFO, they’ll use the $15 flour first – perfect for accurate cost tracking and fresh product management.
2. Chronological Organization Tools
The Date Selection feature isn’t just a calendar – it’s your inventory timeline organizer.
Why Dates Matter in FIFO:
- Creates a clear first-in sequence
- Helps prevent inventory aging
- Ensures proper rotation
Industry Example: A paint supplier tracks three batches:
- Oldest: Industrial paint mixed on March 1
- Middle: Custom colors created March 15
- Newest: Specialty finishes from March 30
The calculator automatically prioritizes the March 1 batch in cost calculations.
3. Quantity and Cost Management
The Units and Cost fields tell your inventory’s value story from start to finish.
Critical Functions:
- Records quantity changes over time
- Tracks cost evolution
- Maintains historical pricing data
Healthcare Supply Example: A medical supplier stocks surgical gloves:
- January batch: 5,000 boxes at $8/box
- February batch: 4,000 boxes at $8.50/box
- March batch: 6,000 boxes at $9/box
When calculating costs, January’s $8 boxes are used first – maintaining accurate cost flow.
4. Automated Layer Valuation
The Total Cost Calculator brings mathematics and chronology together.
Modern Applications: A technology retailer tracking smartphone inventory:
- Wave 1: 50 units × $400 = $20,000
- Wave 2: 75 units × $425 = $31,875
- Wave 3: 100 units × $450 = $45,000
The calculator maintains these distinct layers while prioritizing older inventory costs.
5. Sales Volume Integration
The Units to Sell input transforms your inventory data into actionable cost information.
Practical Scenarios: Fresh Produce Wholesaler
- Morning Stock: 1,000 kg
- Midday Addition: 500 kg
- Evening Delivery: 750 kg
When selling 1,200 kg, the calculator automatically pulls from morning stock first, following nature’s first-in, first-out pattern.
Results and Analytics
The calculator’s output section provides clarity on your inventory flow and costs.
Case Study: Fresh Juice Production Starting Inventory:
- Early Morning Batch: 500 bottles at $2/bottle
- Mid-Morning Batch: 600 bottles at $2.20/bottle
- Afternoon Batch: 400 bottles at $2.50/bottle
When selling 800 bottles:
- First 500 bottles use early morning costs ($2 × 500 = $1,000)
- Next 300 bottles use mid-morning costs ($2.20 × 300 = $660) Total COGS = $1,660
By understanding these components, you can effectively use the FIFO Inventory Calculator to optimize inventory valuation, enhance financial accuracy, and make strategic business decisions.
Mastering FIFO: Strategic Advantages & Key Limitations You Need to Know
The First-In, First-Out (FIFO) method offers a practical, reliable approach to inventory management, but like any methodology, it comes with its pros and cons. Here’s a breakdown to help you determine how FIFO can work for your business.
The Benefits of Using FIFO
Natural Inventory Flow for Perishable Goods
FIFO aligns with the way many businesses naturally sell or use products. In industries like food, beverages, or pharmaceuticals, FIFO ensures older inventory is sold first, minimizing the risk of spoilage or expiration. This method supports freshness and compliance with health regulations.
Lower COGS During Inflation = Higher Profits
During inflationary periods, older (and typically cheaper) inventory is used first. This results in a lower Cost of Goods Sold (COGS), which can increase your gross profit margins. Businesses focused on showing higher profitability often favor FIFO for this reason.
Reduces Waste and Obsolescence
FIFO helps businesses prevent inventory from sitting idle. Older stock is prioritized for use or sale, reducing the chances of waste and the write-offs of outdated inventory. This is particularly important for seasonal or fast-moving industries like fashion and technology.
The Limitations of Using FIFO
Higher Taxable Income in Rising Markets
While FIFO might result in higher profits, this also means higher taxable income. Businesses must prepare for increased tax liabilities, especially in inflationary environments.
Mismatch with Physical Inventory Flow
For industries dealing with non-perishable items (e.g., machinery or furniture), FIFO may not reflect the actual physical flow of inventory. In such cases, the recorded costs might not align with the true movement of goods.
Complexity in Valuation for Large Inventories
Businesses with vast or diverse inventory might find managing FIFO layers cumbersome, especially without automation tools.
FIFO is an excellent method for industries prioritizing freshness and reducing waste. However, businesses should weigh their profitability benefits against their potential tax implications and operational complexities.
FIFO vs. Other Inventory Valuation Methods: Choose the Right Approach
Deciding between FIFO, LIFO, or Weighted Average requires understanding the distinct advantages and drawbacks of each method. Here’s a comparative look to help you choose the best approach for your business.
Aspect | FIFO (First-In, First-Out) | LIFO (Last-In, First-Out) | Weighted Average |
Inventory Prioritization | Oldest stock sold first. Ideal for perishable goods. | Newest stock sold first. Works well in inflationary environments. | Costs spread evenly across all inventory. |
COGS Impact | Lower COGS during inflation; higher profitability. | Higher COGS during inflation; lower taxable income. | Average cost makes profitability predictable. |
Complexity | Requires tracking layers but aligns with natural stock flow. | Needs precise tracking of the newest inventory layers. | Simplifies tracking without layers. |
Industry Use | Food, healthcare, tech (products with shelf life or rapid turnover). | Industrial goods, fuel (when inflation benefits cost savings). | Broad use in industries prioritizing simplicity. |
Tax Implications | May increase taxable income in rising price environments. | Reduces taxable income during inflation. | Neutral tax implications. |
Valuation Accuracy | Highly accurate for reflecting real-time inventory movement. | Less accurate for real-time tracking but benefits financial strategy. | Moderate accuracy with fewer fluctuations. |
Key Considerations
- Choose FIFO if your priority is reflecting the natural flow of inventory, particularly for perishable or rapidly moving goods.
- Opt for LIFO if minimizing tax liability in inflationary markets is a priority.
- Select Weighted Average for simplicity in inventory management and steady valuation without worrying about layers.
Pro Tip: Combine these methods with robust inventory software for streamlined management and precise reporting.
Overcoming FIFO Challenges: Practical Solutions for Seamless Inventory Management
Implementing the First-In, First-Out method can revolutionize inventory management, but like any strategy, it comes with its own set of challenges. Here, we tackle common obstacles businesses face and offer actionable solutions to ensure smooth implementation.
📦 Inventory Layer Complexity
Challenge: Managing multiple inventory layers feels like solving a puzzle with too many pieces.
Strategic Solutions:
- Implement smart inventory software that automatically tracks layer movements
- Utilize cloud-based ERP systems for real-time inventory visibility
- Create digital dashboards for at-a-glance layer monitoring
- Set up automated alerts for inventory level changes
🔄 Physical Flow Alignment
Challenge: Your physical storage doesn’t match your FIFO calculations.
Winning Strategies:
- Design storage layouts that promote natural FIFO flow
- Install flow-through racking systems for automatic rotation
- Implement color-coded labeling for different inventory batches
- Create dedicated picking zones for older inventory
📊 Data Accuracy
Challenge: Keeping records aligned with actual inventory movements.
Smart Solutions:
- Deploy barcode scanning systems for accurate tracking
- Conduct regular cycle counts to verify inventory levels
- Maintain detailed batch records with date stamps
- Implement cross-checking procedures for data entry
To overcome these challenges holistically, combine technology with training. Automation tools are powerful, but their effectiveness depends on how well employees understand and implement FIFO procedures. Regular audits and adjustments ensure alignment between recorded and physical inventory.
Maximize Inventory Insights and Simplify Stock Handling
The FIFO Method Calculator is your ultimate tool for optimizing inventory management. By prioritizing the sale or use of your oldest stock, FIFO ensures better cost accuracy, minimizes waste, and enhances financial clarity.
Whether you’re managing seasonal goods, perishable items, or tech products, this approach provides actionable insights to streamline your operations and boost profitability. From detailed inventory tracking to precise Cost of Goods Sold (COGS) calculations, it empowers businesses to make smarter decisions with ease.
Paired with automation tools and effective storage practices, FIFO can revolutionize how you handle stock. Take control of your inventory today and unlock the potential for more efficient, profitable, and sustainable business operations.