How High Can You Stack Pallets in a Warehouse? Essential Tips for Warehouse Efficiency
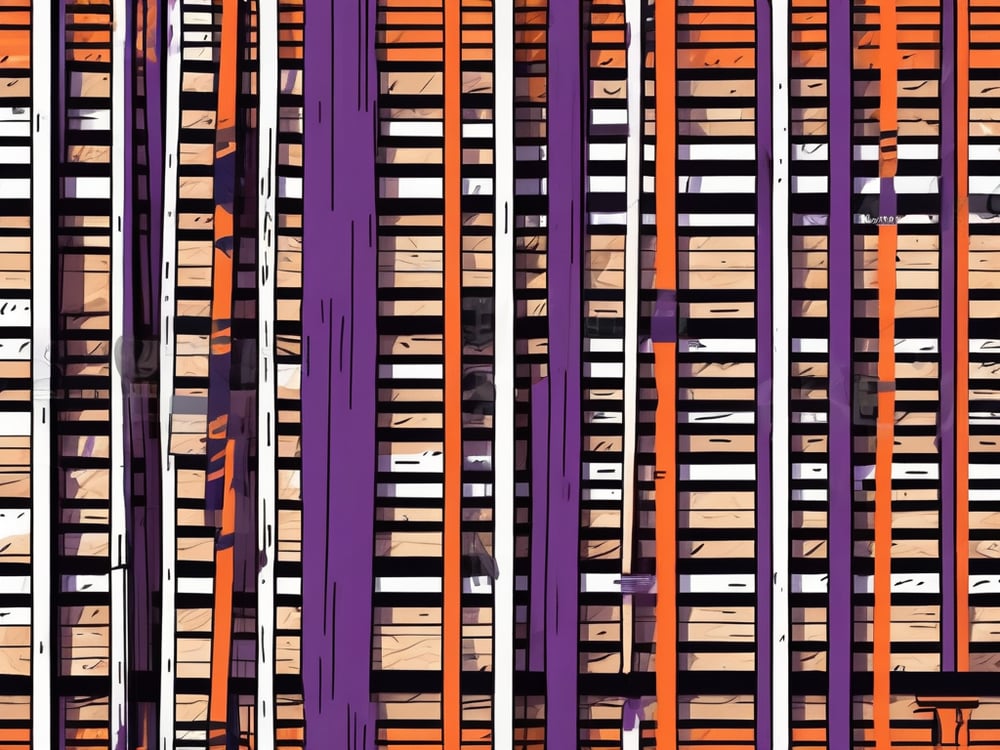
Did you know that the Guinness World Record for the highest pallet stack is a mind-boggling25.08 meters? That’s taller than a 7-story building!
While achieving such heights may be an impressive feat, it’s essential to understand the regulations, factors, and safety measures involved in pallet stacking to ensure a well-organized and secure warehouse environment.
Let’s dive in and find out just how high can pallets be stacked in a warehouse.
Optimal Pallet Stacking Heights for Warehouse Efficiency
Determining the optimal height for stacking pallets in a warehouse is crucial for maximizing space efficiency while ensuring safety and operational effectiveness. Here’s a detailed look at the factors that influence the best stacking height
- Structural Integrity and Design of the Warehouse:
- Load-Bearing Capacity:
- The warehouse’s racking system must be designed to handle the weight of stacked pallets. This includes evaluating the strength of beams and columns to prevent collapse.
- Consultation with Structural Engineers: Engaging with engineers can help determine the safe limits based on the specific design and load capacity of your warehouse. For businesses managing high-volume inventory, leveraging 3PL services in the USA can help optimize warehouse operations and ensure efficient pallet stacking strategies.
- Ceiling Height:
- The height of the warehouse ceiling influences how high you can stack pallets. A higher ceiling allows for greater stacking, but the racking system must be compatible with this height.
- Load-Bearing Capacity:
- Type of Racking System:
- Selective Racking:
- This type provides easy access to each pallet but may limit stacking height due to stability concerns. Typically suitable for moderate heights.
- Drive-In/Drive-Through Racking:
- Ideal for high-density storage and allows for higher stacking. However, careful planning is needed to ensure safe forklift access and efficient operation.
- Push-Back Racking:
- Allows for higher stacking by utilizing a system that pushes pallets backward. It’s suitable for high-density storage but requires specific design considerations.
- Selective Racking:
- Pallet Characteristics:
- Load Distribution:
- Proper distribution of weight across the pallet and the racking system is essential. Overloading lower levels can affect stability and limit stacking height.
- Pallet Material and Quality:
- High-quality, sturdy pallets can support greater heights. Ensure pallets are in good condition to prevent collapse.
- Load Distribution:
- Safety Regulations and Compliance:
- OSHA Standards:
- Follow Occupational Safety and Health Administration (OSHA) guidelines which provide limits and safety measures for stacking heights.
- Local Codes:
- Adhere to local building codes and regulations which may impose additional restrictions on stacking heights for safety reasons.
- OSHA Standards:
- Operational Efficiency:
- Forklift Accessibility:
- Ensure that stacking heights allow forklifts to access and retrieve pallets without obstruction. Excessive height can hinder operational efficiency and increase accident risk.
- Warehouse Layout:
- The layout should facilitate easy movement and avoid blockages in aisles and emergency exits. Proper planning helps in maintaining a safe and efficient workspace.
- Forklift Accessibility:
By carefully considering these factors, you can determine the optimal height for stacking and reap the benefits of pallets to the full extent. This ensures effective use of warehouse space while maintaining a safe and operational environment.
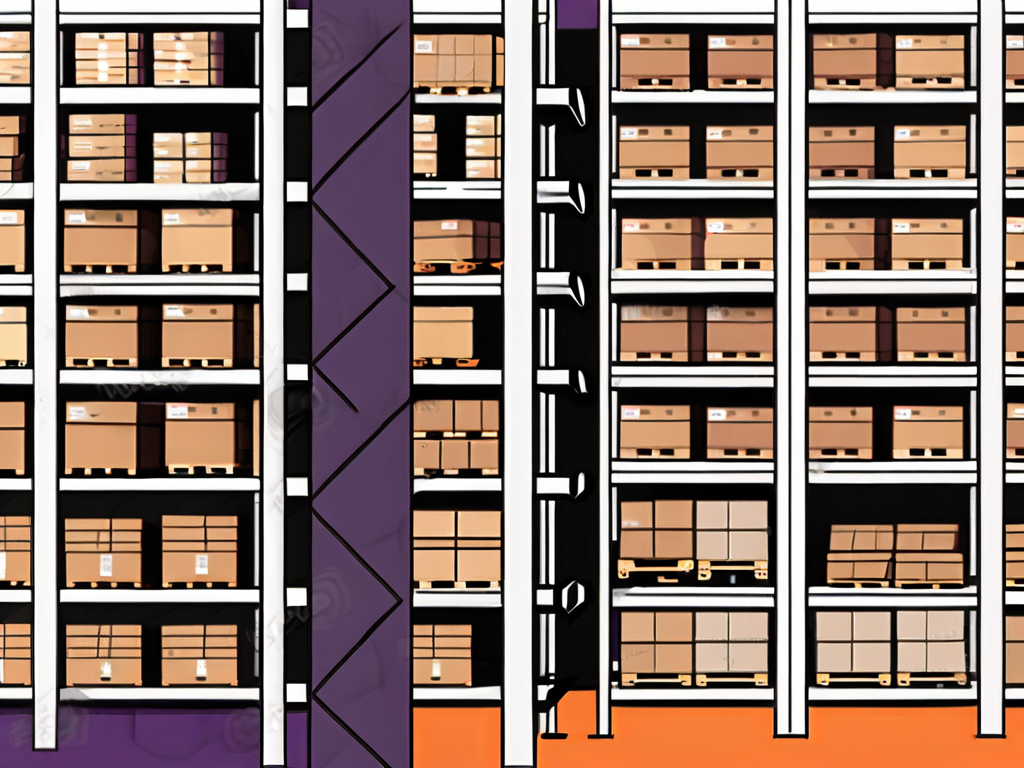
Factors Determining Pallet Stacking Height
When it comes to determining the height at which pallets can be stacked in a warehouse, several factors come into play. Understanding optimal stacking heights is crucial for warehouse safety. Read more about how to choose a warehouse service provider for your business needs. Let’s dive into these crucial considerations.
Pallet Design and Material
The design and material of the pallet itself have a significant impact on how high it can be safely stacked. Pallets made from sturdy materials, such as hardwood or plastic, can generally withstand greater weight and pressure compared to those made from weaker or less durable materials.
Additionally, the design of the pallet, including factors like deckboard and stringer configurations, can also influence its stacking height capacity. Pallets with closely spaced deckboards and solid stringers provide better support for goods and allow for higher stacking without compromising stability.
Weight of the Goods
The weight of the goods being stacked on the pallets is another critical factor to consider.
Heavier items can put more strain on the pallet and the overall stack, potentially compromising its stability. Warehouse staff must be aware of weight limits and ensure that they are not exceeded to maintain a safe stacking height.
Moreover, the distribution of weight across the pallet surface is essential. Concentrated heavy loads or unevenly distributed goods can create pressure points that weaken the pallet’s structural integrity, limiting the safe stacking height.
Warehouse Ceiling Height
The height of the warehouse ceiling plays a significant role in determining how high pallets can be stacked. Ideally, there should be enough clearance between the topmost pallet and the ceiling to avoid any damage or potential accidents. It’s crucial to take into account the height of both the pallet and the goods when considering the warehouse’s ceiling height limitations.
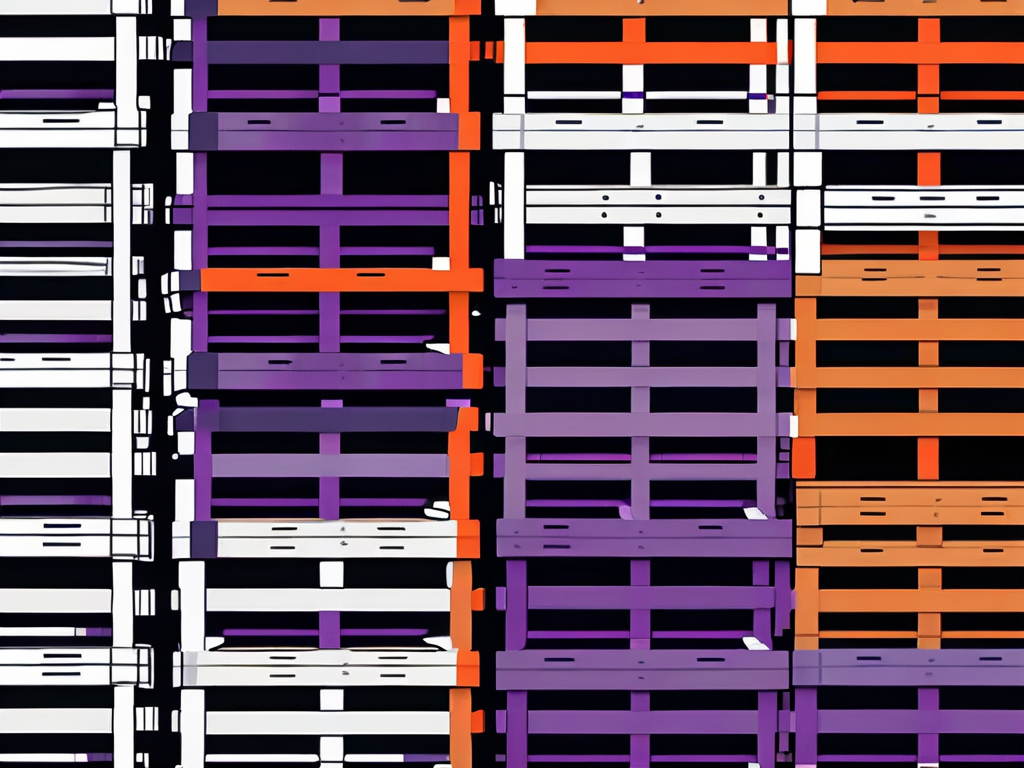
Furthermore, the type of storage system used in the warehouse, such as selective racking or double-deep racking, can also impact the stacking height.
Different racking systems have varying height capacities and clearance requirements, influencing how high pallets can be safely stored within the warehouse.
Safety Measures in Pallet Stacking
To ensure the well-being of warehouse staff and the integrity of the goods stored, safety measures must be implemented when stacking pallets. Regular warehouse inspections and proper training ensure the safe handling of palletized inventory. Discover Fulfyld’s pick and pack fulfillment services for organized inventory management.
Let’s explore some essential practices:
Training for Warehouse Staff
Proper training is key to creating a safe working environment. Warehouse staff should receive comprehensive training on how to stack pallets safely, including:
- understanding weight limits
- following storage regulations
- using equipment correctly
Ongoing training programs can help reinforce best practices and keep safety at the forefront.
Training sessions can also include simulations or hands-on practice to ensure that staff members are well-equipped to handle various stacking scenarios. By familiarizing themselves with different pallet sizes, weights, and stacking configurations, employees can enhance their skills and minimize the risk of accidents or injuries.
Regular Safety Inspections
Performing regular safety inspections is crucial in identifying any potential hazards or issues that may compromise the integrity of pallet stacking. The inspections should cover everything from the condition of pallets and racks to evaluating the overall stability of stacked pallets. Any problems or concerns should be addressed promptly to maintain a safe working environment.
During safety inspections, it is also important to assess the organization and layout of the warehouse to ensure that aisles are clear, emergency exits are unobstructed, and safety signage is visible. By maintaining a tidy and organized workspace, the risk of accidents due to clutter or poor visibility can be significantly reduced.
Optimizing Warehouse Space with Pallet Stacking
Efficient space utilization is a top priority for warehouses, and pallet stacking allows for vertical optimization. Efficient space utilization is a top priority for warehouses, and proper pallet stacking helps maximize storage. Learn how Fulfyld’s 3PL services can improve warehouse efficiency.
Let’s explore the benefits and drawbacks of maximizing space through pallet stacking:
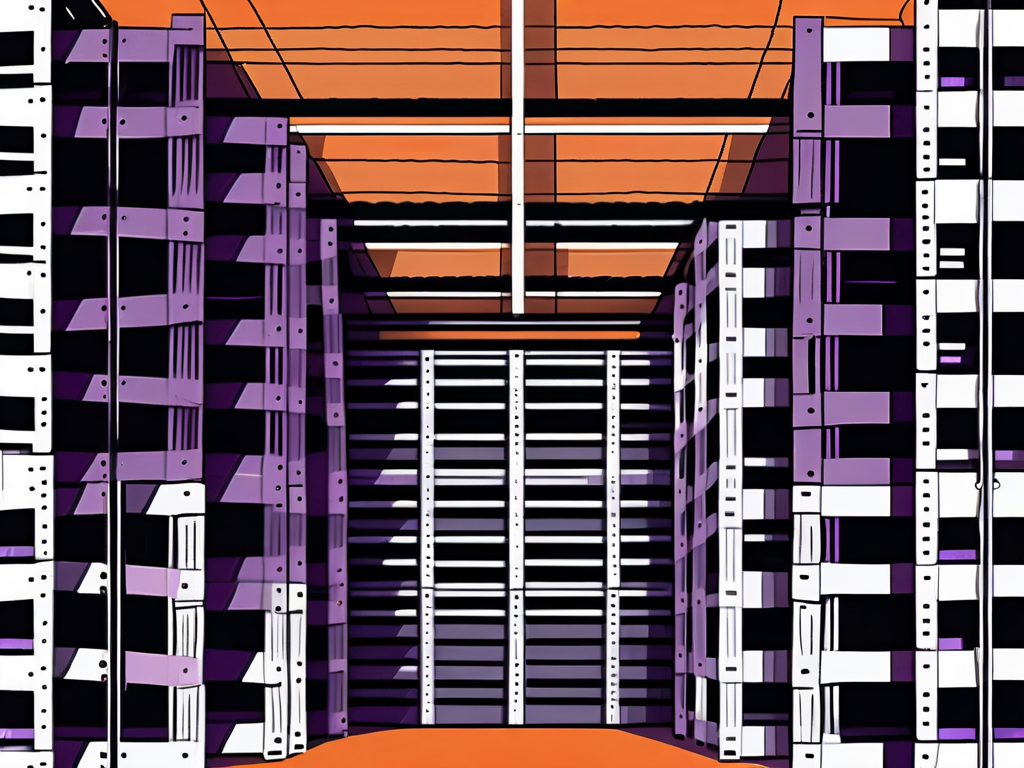
Benefits of Vertical Stacking
Vertical stacking allows warehouses to make the most of the available space by utilizing the warehouse’s height.
- This strategy maximizes storage capacity, allowing for more products to be housed within the same footprint.
- It can also streamline the retrieval process, as products can be organized and accessed more efficiently.
- Moreover, vertical stacking can enhance inventory management by facilitating better tracking and rotation of goods.
By organizing products in a vertical manner, warehouses can implement a first-in, first-out (FIFO) system more effectively, ensuring that older stock is used before newer items. This practice reduces the risk of product expiration and minimizes waste, ultimately leading to cost savings for the warehouse.
Drawbacks of Over-stacking
While pallet stacking offers many benefits, over-stacking can lead to potential problems. Excessively high stacks can increase the risk of pallet collapse, creating safety hazards and damaging goods. It’s important to strike the right balance between maximizing storage space and ensuring the stability and integrity of the stacked pallets.
Furthermore, over-stacking can impede accessibility and retrieval efficiency. In a densely packed warehouse with overly tall stacks, reaching products on higher shelves can become challenging and time-consuming.
This can slow down operations, increase labor costs, and even result in errors during picking and packing processes. Warehouse managers must consider the trade-offs between space optimization and operational efficiency to maintain a well-functioning and safe warehouse environment.
Over-stacking pallets can cause inefficiencies and damage inventory. Learn how real-time inventory can improve supply chain efficiency.
Technological Innovations in Pallet Stacking
As technology continues to advance, it is no surprise that pallet stacking has also seen its fair share of innovation. Let’s explore some exciting technological advancements in this area:
Automated Stacking Systems
Gone are the days of manually stacking pallets, thanks to automated stacking systems. These systems use robotics and advanced algorithms to arrange pallets in an optimal and secure manner. Not only do they enhance efficiency, but they also reduce the risk of human error and ensure uniformity in stacking patterns.
Imagine a warehouse bustling with activity, where robotic arms seamlessly glide across the floor, swiftly and precisely stacking pallets one on top of the other. These automated stacking systems not only save time but also minimize the physical strain on workers, leading to a safer and more ergonomic work environment.
Future Trends in Pallet Stacking
The future of pallet stacking holds great promise, with advancements such as smart sensors, which can monitor the stability and weight distribution of stacked pallets in real-time. This technological integration aims to further enhance safety, optimize space utilization, and streamline warehouse operations.
Picture a warehouse equipped with smart sensors embedded within the pallet racks, constantly collecting data on the weight distribution and structural integrity of the stacked pallets. This real-time monitoring allows for immediate adjustments to be made in case of any instability, preventing accidents and ensuring a more efficient use of warehouse space.
Balancing Height and Safety for Optimal Warehouse Efficiency
Stacking pallets in a warehouse is not just about piling them high. It requires careful consideration of regulations, factors, and safety measures.
Adhering to warehouse storage regulations, understanding the factors that influence stacking height, implementing safety measures, and embracing technological innovations all contribute to a well-organized and secure warehouse environment.
By finding the right balance between maximizing space and maintaining stability, warehouses can truly elevate their storage capabilities. For expert warehouse management and fulfillment solutions, Fulfyld provides tailored logistics support to optimize storage efficiency and safety.