Did you know that unsecured pallet racking can pose serious safety risks in a warehouse? According to a study by the Occupational Safety and Health Administration, over 4000 injuries occur each year due to accidents related to unsecured racking.
It’s clear that ensuring the stability and security of your pallet racking is crucial for the safety of your employees and the efficiency of your operations. In this blog post, we will learn:
- How to secure pallet racking
- How to choose the right fasteners
- How to prepare the warehouse floor for installation
- When to perform regular maintenance and inspection of secured pallet racks
Table of Contents
ToggleStep-by-Step Guide to Securing Pallet Racking
Follow these steps and rest assured knowing that your pallet racking system is securely installed and ready for use. Here are the steps you need to take:​
1. Positioning the Racks
- Align Racks:Â Carefully position each rack in its designated location, aligning it with the marked installation points on the floor.
- Check Level:Â Use a level to ensure that the racks are straight and plumb. This step is crucial for maintaining the integrity and stability of the racking system.
- Consider Layout Factors:Â Account for load distribution, forklift accessibility, and proximity to other structures. Ensure the layout maximizes storage space while ensuring safety and efficiency.
- Plan for Future:Â Consider any future expansion plans or changes in inventory to optimize the racking configuration.
2. Drilling and Fastening Process
- Drill Holes:Â With the racks in position, use a drill with the appropriate-sized masonry bit to create holes in the concrete floor at the designated anchor points.
- Insert Anchor Bolts: Insert the anchor bolts into the drilled holes and tighten them with a wrench or socket set. Follow the manufacturer’s instructions for proper installation.
- Choose Appropriate Bolts:Â Ensure the anchor bolts can support the weight of the stored items. Consider factors such as seismic activity, environmental conditions, and operational requirements.
- Inspect and Maintain:Â Regularly inspect and maintain the anchor bolts to ensure continued safety and stability.
3. Secure All Racks
- Repeat Process:Â Repeat the drilling and fastening process for each rack, double-checking the alignment and level as you go.
- Final Check:Â Once all the anchor bolts are securely tightened, verify the stability and alignment of the entire racking system.
Safety Concerns with Unsecured Pallet Racking
Unsecured pallet racking can lead to several critical issues that impact safety, efficiency, and overall operations within a warehouse. Some of the safety concerns are:
- Risk of Collapse:Â The racking can collapse, posing serious dangers to employees, causing significant damage to stored products, resulting in financial losses, and jeopardizing customer satisfaction.
- Accidents Due to Misalignment:Â When racking is not properly anchored, it can become unstable and shift, leading to collisions with forklifts or other equipment, which puts operators and pedestrians at risk of injury.
- Inefficient Use of Space:Â Unsecured racking can lean or tilt, causing uneven weight distribution. This not only increases the risk of collapse but also limits the amount of weight that can be safely stored on each shelf, reducing overall storage capacity.
- Inventory Management Issues:Â Unstable racking can cause products to fall off and become disorganized, leading to inventory errors, misplaced items, and difficulties in locating specific products. This results in delays in order fulfillment and decreased productivity.
Efficiency and Organization Benefits
Besides the safety aspect, securing pallet racking also offers numerous efficiency and organizational benefits. When the racking is securely fastened to the warehouse floor, it provides a stable and reliable storage solution. This makes it easier for employees to locate and retrieve items, improving overall efficiency.
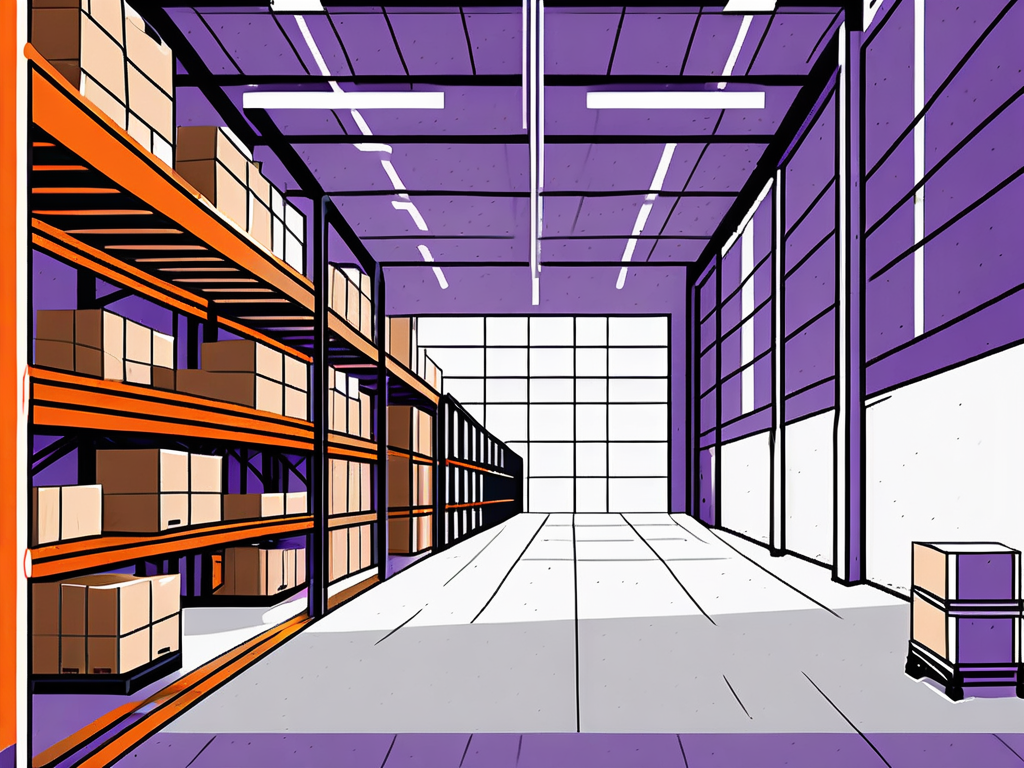
Furthermore, a secured racking system allows for better organization and utilization of space. Properly aligned racks ensure that every inch of the warehouse is maximized, reducing wasted space and increasing storage capacity. This can be especially important for businesses with limited warehouse space.
Moreover, a well-secured pallet racking system can also contribute to a more streamlined inventory management process.
By having a structured storage system in place, businesses can implement efficient inventory tracking methods, such as barcode scanning or RFID technology. This not only helps in maintaining accurate stock levels but also enables faster order fulfillment and reduces the risk of stockouts.
Additionally, a securely fastened racking system promotes a safer working environment by reducing the chances of accidents caused by unstable storage units.
This not only protects employees from potential injuries but also safeguards the inventory from damage due to falls or collapses. By prioritizing safety through proper racking installation, businesses can enhance their overall operational efficiency and maintain a reliable storage infrastructure for long-term success.
Materials Needed for Securing Pallet Racking
Securing pallet racking requires a few essential materials. Let’s take a look at what you’ll need to get the job done:
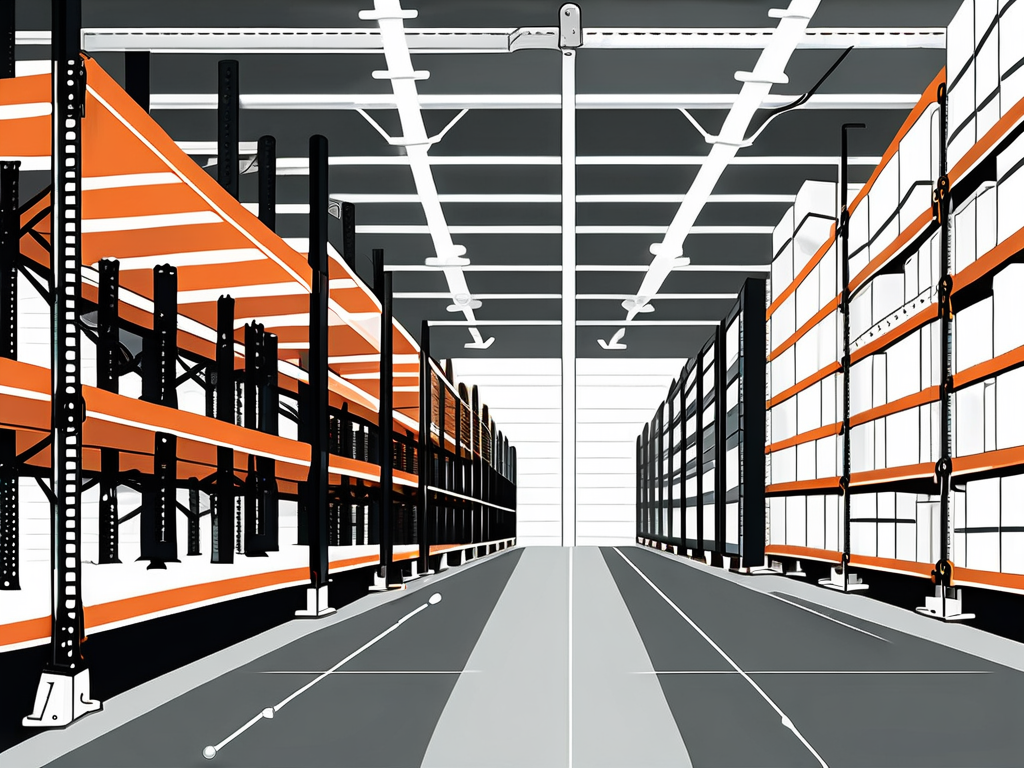
Overview of Necessary Tools
- Drill: You’ll need a drill to create holes in the concrete floor for the anchor bolts.
- Wrench or Socket Set:Â To tighten the anchor bolts and ensure a secure fit.
- Measuring Tape:Â Essential for accurately marking the installation points on the floor.
- Safety Gear: Don’t forget to wear appropriate personal protective equipment, such as safety glasses and gloves, while working.
Additionally, having a level on hand can help ensure that your pallet racking is installed evenly and securely. This tool will help you make sure that the racking is straight and stable, minimizing the risk of accidents or collapses.
Choosing the Right Fasteners
When it comes to securing pallet racking, choosing the right fasteners is crucial. The type of fastener you use depends on the type of flooring in your warehouse.
For concrete floors, anchor bolts are the most popular choice due to their strength and durability. However, if you have a different type of flooring, such as wood or metal, you’ll need to select fasteners that are suitable for that specific material.
It’s important to consider the weight capacity of your pallet racking system when selecting fasteners. Make sure the fasteners you choose are capable of supporting the weight of the loaded pallets to prevent any structural failures.
Additionally, consulting with a professional or structural engineer can provide valuable insights into the best fastening options for your specific warehouse setup.
Preparing the Warehouse Floor for Installation
Before you can start securing your pallet racking, it’s important to prepare the warehouse floor properly. Ensuring a solid foundation for your racking system is crucial for its stability and longevity.
By taking the time to follow these steps, you can create a safe and efficient storage space for your inventory.
Cleaning and Clearing the Area
Begin by clearing the area around the installation points of any debris or obstacles. This step is essential to guarantee that the racking can be properly positioned and anchored without any obstructions.
Removing any clutter or dirt from the floor not only facilitates the installation process but also enhances the overall cleanliness and organization of the warehouse.
Moreover, a clean and clear workspace promotes a safer environment for your employees, reducing the risk of accidents and injuries. By prioritizing cleanliness in your warehouse, you demonstrate a commitment to both efficiency and safety in your operations.
Marking the Installation Points
Using a measuring tape, determine the exact locations where the racking will be installed. Precision is key in this step to ensure that the racking system fits seamlessly into your warehouse layout.
By marking these points on the floor with a marker or tape, you establish a visual guide for the installation process.
Consideration of various factors such as the dimensions of the pallets, the required clearance for forklifts, and adherence to safety regulations is paramount.
Proper planning and attention to detail during this phase can prevent costly mistakes and streamline the installation process.
By meticulously marking out the installation points, you set the stage for a well-organized and functional warehouse space.
Regular Maintenance and Inspection of Secured Pallet Racks
Securing your pallet racking isn’t a one-time task; it requires regular maintenance and inspection to ensure ongoing safety and efficiency. Follow this routine inspection checklist to keep your racks in optimal condition:
Routine Inspection Checklist
- Check for any signs of damage, such as bent or cracked components.
- Inspect the anchor bolts to ensure they are still tightly secured.
- Look for any signs of misalignment or shifting, such as crooked or uneven racks.
- Remove any obstructions or debris that may have accumulated around the racking.
- Ensure that the weight load on the racks is distributed evenly and within the recommended limits.
Addressing and Fixing Common Issues
If you notice any issues during your inspection, it’s important to address them promptly. Bent or damaged components should be replaced to maintain the integrity of the racking system.
If misalignment or shifting occurs, it may be necessary to reposition and re-anchor the affected racks. Regular maintenance and timely repairs will help extend the lifespan of your pallet racking and minimize safety risks.
Ensuring Long-Term Safety and Efficiency
Securing pallet racking to the warehouse floor is a critical task that should not be taken lightly. By understanding the importance of proper installation and investing in routine maintenance, you can ensure a safe and efficient working environment for your employees while maximizing the space in your warehouse.
Remember, a secure racking system is the foundation of a well-organized and productive warehouse.