Kitting is a crucial process in fulfillment centers that involves assembling individual items into ready-to-ship kits. Understanding how the kitting process works in a fulfillment center is essential for optimizing order fulfillment and ensuring customer satisfaction.
Kitting involves bundling multiple products into a single package, streamlining the assembly and shipping process. By efficiently organizing and preparing these kits, fulfillment centers can reduce errors, speed up delivery times, and enhance the overall customer experience.
This article will cover the following key points:
- Understanding the kitting process in fulfillment centers
- Benefits the kitting processÂ
- Common obstacles in the kitting process
Table of Contents
ToggleEverything You Need to Know About the Kitting Process in Fulfillment Center
Kitting is a meticulous process that requires careful attention to detail and efficient inventory management. The success of the kitting process relies on the seamless execution of several key steps, ensuring that each kit is assembled accurately and efficiently.
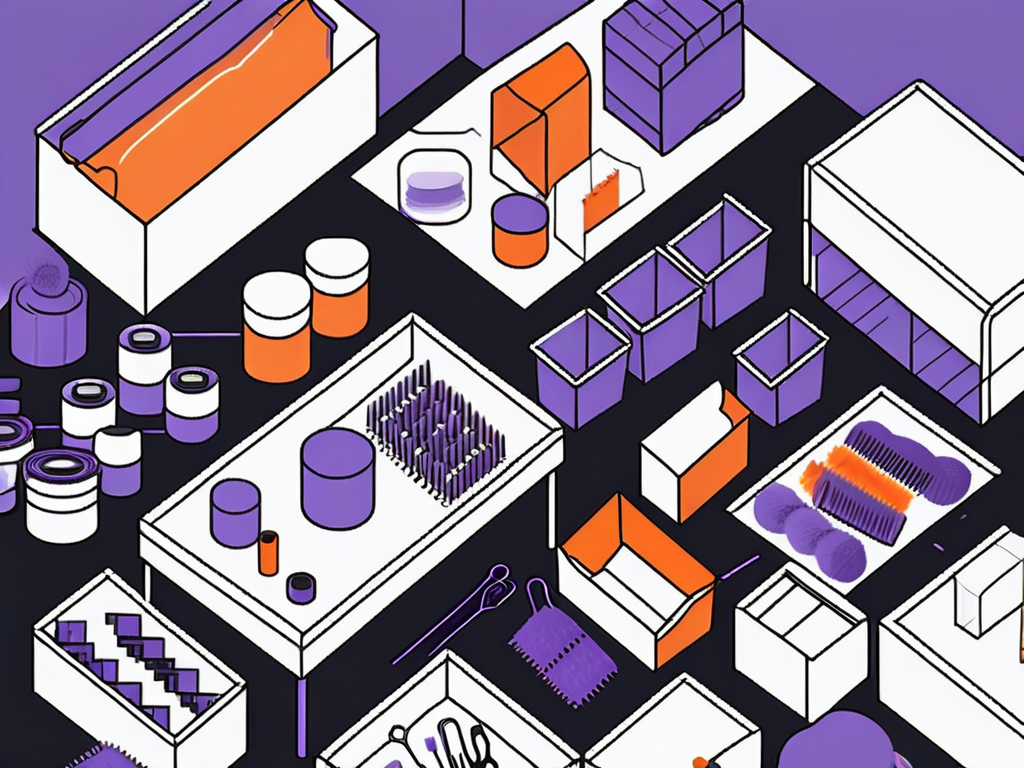
Gathering the Components
The kitting process begins with collecting all required components from inventory. Effective inventory management ensures all parts are available and prevents delays. Next, components are grouped according to kit specifications, ensuring completeness. Quality control is crucial—damaged or defective items are promptly replaced, maintaining high standards for each kit.
Assembling the Kit
Once components are gathered, skilled workers assemble the kit, carefully combining items into a customer-ready package. Some of the roles of a kit are:
- ensure proper fitting
- secure connections
- include any necessary instructions
Experienced technicians follow strict guidelines and use specialized tools to ensure precision and accuracy in every assembly.
Quality Control and Inspection
After assembly, each kit undergoes rigorous quality control. This process includes visual inspections and functional tests to ensure all components are correct and in good condition. Quality control specialists meticulously check each kit for accuracy and defects, following strict protocols to meet customer specifications.
Packaging and Shipping
The final step in kitting is packaging and shipping. Kits are securely packed with materials like boxes and bubble wrap to protect their contents. They are then labeled and prepared for dispatch, with the logistics team ensuring timely delivery.
Multiple kits may be consolidated for efficiency, and a final inspection ensures each package is sealed and labeled correctly, reflecting the best packaging for efficient shipping. This thorough process guarantees that customers receive their products in perfect condition, enhancing their overall experience.
The Benefits of Kitting in a Fulfillment Center
Now that we have explored the kitting process, let’s discuss the significant benefits it brings to a fulfillment center.
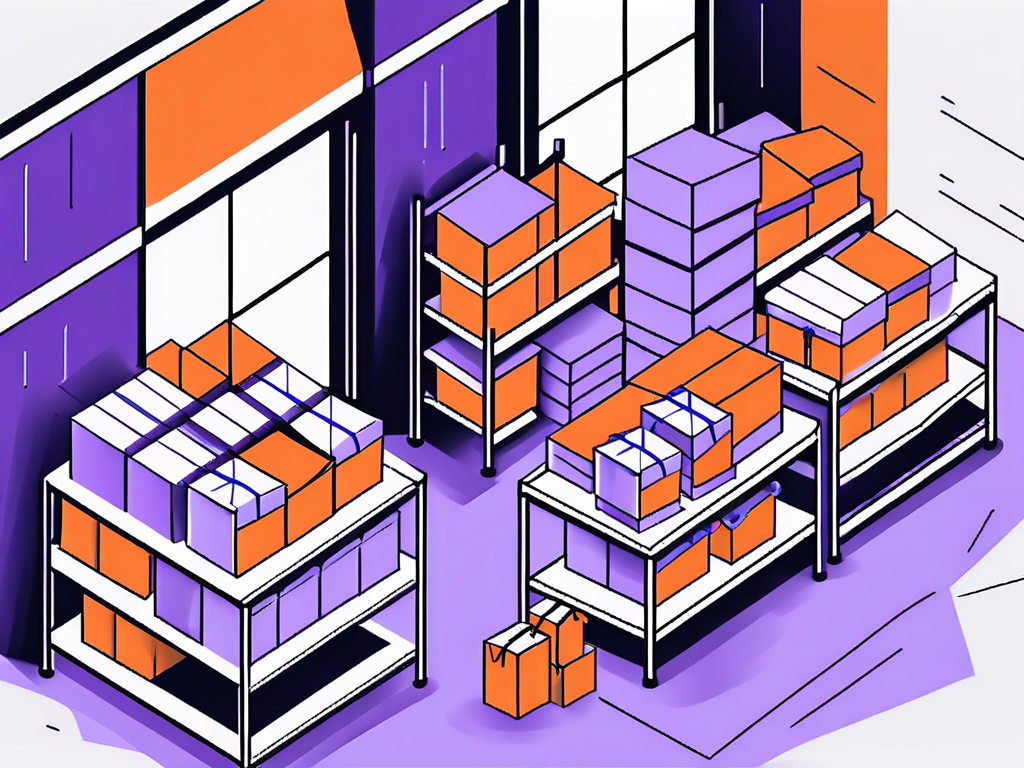
Efficiency in Order Processing
Kitting boosts order processing efficiency by combining components into pre-assembled kits. This approach simplifies:
- Picking
- Packing
- Shipping
For instance, in a fulfillment center using kitting, workers assemble kits with all required items, streamlining the workflow and reducing time spent searching for individual components. This not only speeds up processing but also minimizes errors, enhancing overall productivity.
Cost Reduction and Savings
Kitting reduces labor costs and minimizes errors by consolidating items into pre-assembled kits. This streamlined approach also optimizes packaging, saving space and lowering shipping costs.
The resulting efficiencies can be reinvested into the fulfillment center or passed on to customers, providing cost savings and competitive pricing.
By adopting kitting, fulfillment centers not only enhance their operations but also attract and retain customers with better value.
Improved Customer Satisfaction
​Kitting and assembly process boosts customer satisfaction by delivering complete, accurate, and ready-to-use orders. When customers receive neatly assembled kits with everything they need, it creates a positive experience and fosters trust.
This efficiency reduces frustrations with missing or incorrect items, enhances brand loyalty, and encourages repeat business.
Challenges in the Kitting Process
While kitting offers numerous advantages, it also comes with its fair share of challenges. Understanding and addressing these challenges is crucial for ensuring a smooth and efficient kitting process.
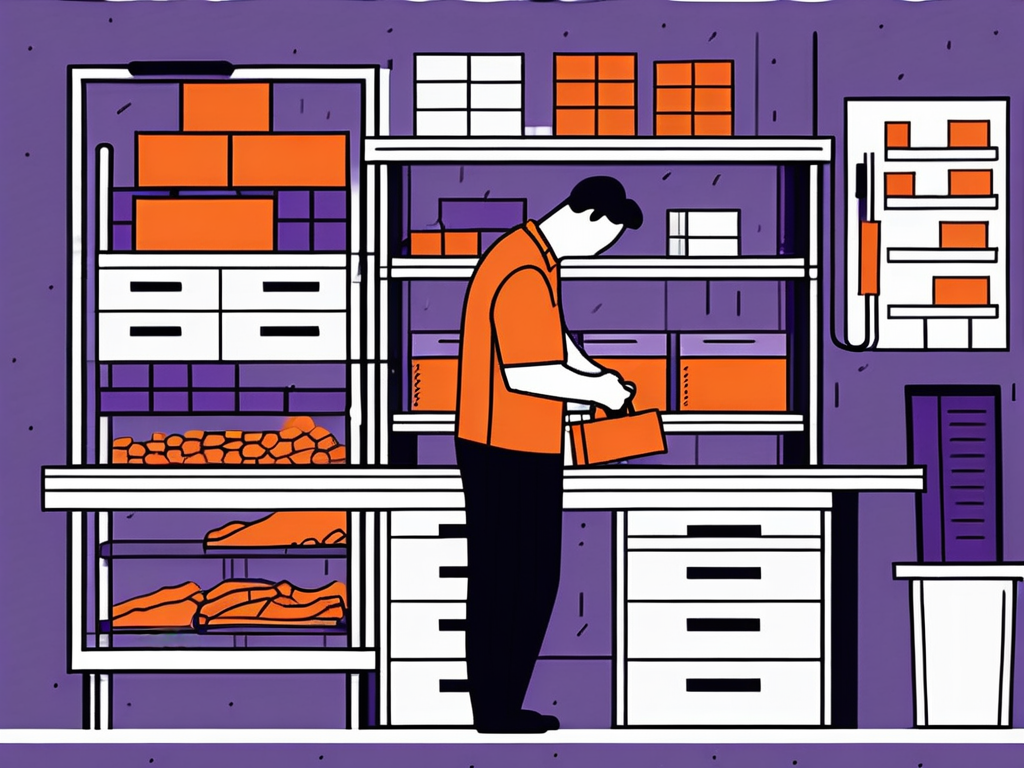
Inventory Management Issues
One of the primary challenges in the kitting process is managing inventory accurately. Assembling kits requires precise tracking of each component to avoid stock imbalances and delays. Key issues include:
- Tracking Each Component:Â Ensuring accurate inventory for every part involved in the kit.
- Monitoring Stock Levels:Â Keeping a close eye on inventory to prevent shortages or overstocking.
- Preventing Bottlenecks:Â Avoiding delays due to missing components or supply chain disruptions.
To overcome these challenges, fulfillment centers must implement robust and smart inventory management systems and efficient tracking mechanisms. Continuous monitoring and proactive inventory control are essential to ensure all necessary components are available when needed.
Quality Assurance Difficulties
Maintaining consistent quality across all assembled kits is another significant challenge. With various components and potential for variation, ensuring each kit meets quality standards requires rigorous processes. This involves:
- Rigorous Inspections:Â Conducting thorough checks to verify the integrity of each kit.
- Functional Tests:Â Ensuring that all components work correctly when assembled.
- Effective Quality Control Processes:Â Implementing robust measures to detect and address any issues before kits are shipped.
Fulfillment centers must focus on meticulous attention to detail and effective quality control to prevent defects and maintain high customer satisfaction.
Handling High Volume Orders
Managing high-volume orders introduces additional complexities to the kitting process. Increased demand and tighter deadlines can strain resources and impact efficiency. Challenges include:
- Increased Demand and Time Constraints:Â Navigating the pressures of fulfilling large volumes quickly.
- Need for Efficient Assembly Processes:Â Ensuring that the assembly line can handle high order volumes without delays.
- Maintaining Quality Control:Â Balancing speed with accuracy to avoid errors.
To address these challenges, fulfillment centers should have scalable systems and sufficient resources in place. Efficient management of both the assembly process and quality control is crucial to handling high-volume orders effectively.
Mastering Efficiency with Kitting: The Fulfillment Center Advantage
Kitting transforms fulfillment centers by streamlining order processing into efficient, pre-assembled kits. It reduces labor costs, minimizes errors, and enhances customer satisfaction with complete, organized shipments.
By streamlining the assembly process and improving accuracy, kitting helps meet high customer expectations and adapt to fluctuating demands. As a result, fulfillment centers can deliver exceptional service and maintain a competitive edge in the fast-paced world of e-commerce.