FDA approval is a crucial step for medical device manufacturers looking to bring their products to market. However, navigating the FDA approval process can be complex and costly.
In this article, we will explore the various factors that contribute to the cost of FDA approval for medical devices and strategies that can help minimize those costs. Dive in and learn:
- FDA approval costs
- Factors influencing these expenses
- Strategies to minimize the expensesÂ
Table of Contents
ToggleBreakdown of FDA Approval Costs for Medical Devices
Obtaining FDA approval for a medical device involves various expenses. Let’s take a closer look at the different cost factors that manufacturers should consider, along with some actual numbers to provide a clearer picture.
Preclinical and Clinical Trial Costs
Prior to conducting clinical trials, manufacturers must invest in preclinical testing to gather data on the device’s safety and performance. This can include animal testing, laboratory experiments, and in vitro studies. Clinical trials, on the other hand, involve testing the device on humans to evaluate its efficacy and safety under controlled conditions.
Cost Estimates:
- Preclinical testing: $10,000 to $500,000
- Clinical trials: $1 million to $10 million, depending on the complexity and duration of the trials
Application and Review Fees
Manufacturers are required to submit an application to the FDA for device approval. This application incurs a fee determined by the type of device and the size of the company. Additionally, the FDA charges review fees, which cover the cost of evaluating the application and ensuring compliance with regulatory requirements.
Cost Estimates:
- 510(k) application fee: Approximately $12,432 (small businesses may qualify for a reduced fee)
- Premarket Approval (PMA) application fee: Approximately $365,657 (small businesses may qualify for a reduced fee)
Post-Approval Monitoring Expenses
Once a device receives FDA approval, manufacturers are still responsible for post-market surveillance. This involves monitoring the device’s performance, addressing any safety concerns, and complying with ongoing reporting requirements.
Cost Estimates:
- Post-market surveillance: $100,000 to $500,000 annually, depending on the complexity of the monitoring required
By understanding these costs and planning accordingly, manufacturers can better navigate the financial landscape of FDA approval and bring their medical devices to market efficiently.
Factors Influencing the Cost of FDA Approval
Several factors can significantly impact the cost of obtaining FDA approval for a medical device. Let’s explore some of the key factors to consider.
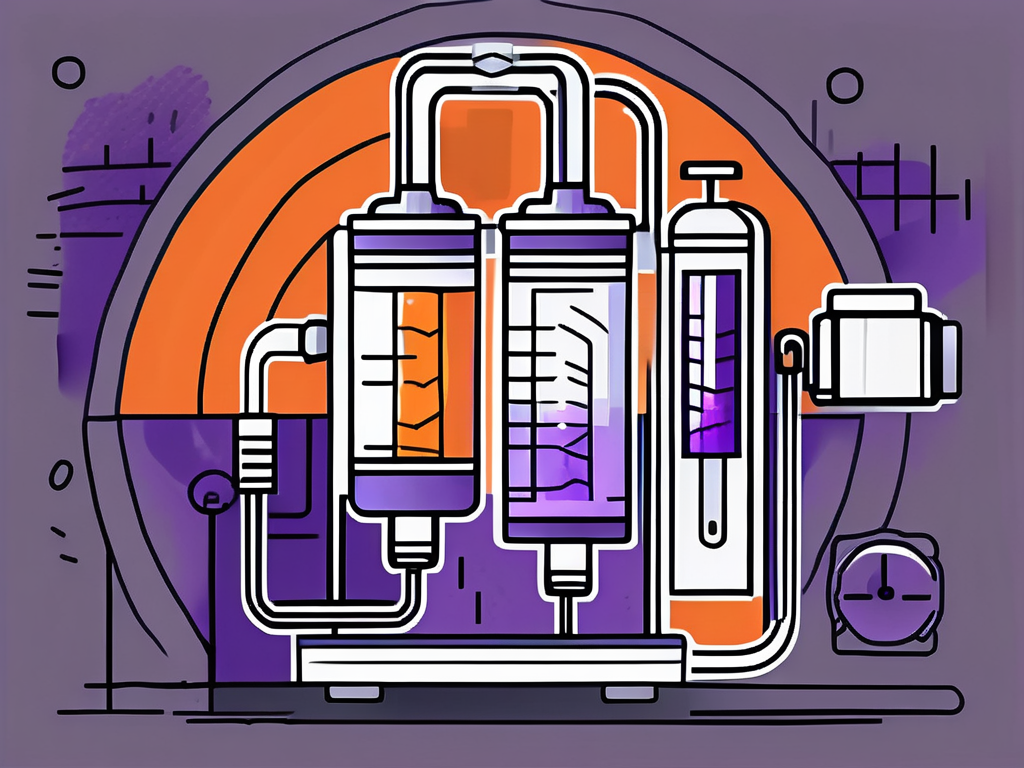
One crucial aspect that can affect the cost of FDA approval is the level of clinical evidence required for the device. The FDA typically requires clinical data to demonstrate the safety and efficacy of a medical device. For devices that are innovative or lack substantial predicate devices, manufacturers may need to conduct extensive clinical trials, which can be a costly and time-consuming process.
Device Classification and Its Impact on Cost
The FDA classifies medical devices into different categories based on the level of risk they pose to patients. Devices in higher-risk categories, such as implantable devices or those used during invasive procedures, may require more extensive testing and scrutiny. Consequently, the cost of obtaining approval for these devices tends to be higher.
Another factor to consider is the need for post-market surveillance and studies. In some cases, the FDA may require manufacturers to conduct post-market studies to monitor the long-term safety and performance of a device. These studies add to the overall cost of FDA approval and require ongoing resources to ensure compliance.
The Effect of Product Complexity on Approval Costs
The complexity of a medical device can also influence the cost of FDA approval. Devices with intricate designs or advanced technologies may require more extensive testing and evaluation. The complexity factor can significantly impact the overall cost and duration of the FDA approval process.
Furthermore, the geographical location of manufacturing facilities can impact approval costs. If a manufacturer has facilities located outside the United States, they may need to comply with additional regulations and requirements to import the device into the country.
This can lead to increased costs associated with ensuring compliance with international standards and regulations.
The Role of Legal and Consultation Fees
Manufacturers often seek legal and consultation services to navigate the FDA approval process effectively. These professionals provide valuable guidance and expertise, but their services come at a cost. Legal and consultation fees should be factored into the overall budget for FDA approval.
In addition to legal and consultation fees, manufacturers must also consider the cost of preparing and submitting the FDA application. This process involves compiling extensive documentation, including:
- Technical specifications
- Clinical data
- Risk assessments
Ensuring the accuracy and completeness of these submissions is crucial to avoid delays in the approval process, adding to the overall cost.
Strategies to Minimize FDA Approval Costs
While obtaining FDA approval for a medical device can be a costly endeavor, there are strategies that manufacturers can employ to minimize these expenses. Let’s dive deeper into some of these strategies and explore additional ways to navigate the complex world of FDA regulations.
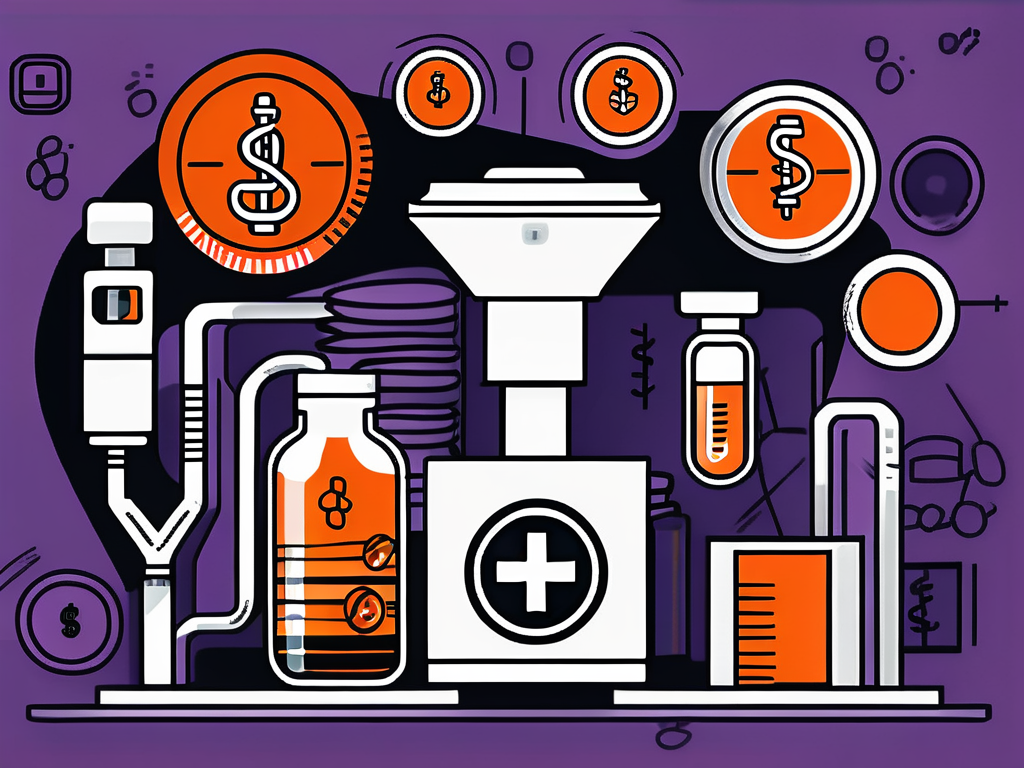
Early and Effective Planning
One of the most effective ways to reduce FDA approval costs is through early and effective planning. By thoroughly understanding the regulatory requirements and timelines, manufacturers can better allocate resources and avoid delays and costly revisions. Working closely with regulatory experts and consultants from the early stages of device development can help streamline the approval process.
Moreover, it is crucial to conduct thorough research and gather comprehensive data during the planning phase. This includes:
- Conducting extensive literature reviews
- Analyzing existing clinical data
- Identifying potential safety and efficacy concerns
By addressing these issues proactively, manufacturers can save both time and money during the FDA approval process.
Leveraging Third-Party Review Programs
Manufacturers can explore third-party review programs authorized by the FDA. These programs involve the use of accredited organizations to assess the safety and effectiveness of medical devices. By leveraging these programs, manufacturers can potentially reduce the review time and associated costs while ensuring compliance with FDA regulations.
Furthermore, collaborating with third-party organizations can provide manufacturers with valuable insights and expertise. These organizations often have a deep understanding of the FDA’s expectations and can guide manufacturers through the complex regulatory landscape. Their input can help manufacturers identify potential pitfalls and address them proactively, minimizing the chances of costly setbacks.
Understanding and Navigating Regulatory Pathways
Another essential strategy to minimize FDA approval costs is a thorough understanding of the available regulatory pathways. Manufacturers should explore the different options for obtaining approval, such as:
- Premarket notifications (510(k))
- Premarket approval (PMA)
- De novo process
Careful consideration of the most appropriate pathway for a specific device can lead to significant cost savings.
It is crucial to note that each regulatory pathway has its own set of requirements and timelines. Manufacturers must conduct a comprehensive analysis of their device’s characteristics and intended use to determine the most suitable pathway.
This analysis should consider factors such as device classification, risk profile, and available clinical data. By selecting the right pathway from the outset, manufacturers can avoid unnecessary expenses associated with switching pathways or addressing unforeseen regulatory challenges.
Navigate FDA Approval with Smart Strategies to Manage Costs
In conclusion, obtaining FDA approval for a medical device is a critical and costly process. While the expenses associated with FDA approval can seem daunting, manufacturers can take proactive steps to minimize costs.
Early planning, leveraging third-party review programs, and understanding regulatory pathways are key strategies in reducing the financial burden. By navigating the FDA approval process efficiently and effectively, manufacturers can bring innovative and safe medical devices to market while managing costs responsibly.