Did you know that effective inventory management can significantly impact a business’s success? According to a study conducted by the National Retail Federation, inventory problems account for nearly $50 billion in losses each year.
It’s clear that accurate inventory levels are vital for maintaining optimal stock levels and avoiding costly overstock or stockout situations. In this article, we will learn:
- How to calculate min/max inventory levels
- How to implement a well-structured min/max inventory system
- The benefits and potential challenges in min/max inventory management
Table of Contents
Toggle3 KEY Steps for Calculating Min/Max Inventory Levels
To calculate min/max inventory levels you must follow these 3 simple steps:
- Gathering Essential Inventory Data:Â The first step is to collect relevant inventory data, including historical sales data, lead times, and safety stock requirements. This data forms the foundation for accurate calculations.
- Analyzing Inventory Turnover Rate:Â Calculate your inventory turnover rate, which measures how quickly inventory is used or sold within a specific period. This analysis helps determine the optimal amount of stock to hold and the rate at which it should be replenished.
- Determining Safety Stock Levels:Â Safety stock acts as a buffer to account for unexpected demand fluctuations or supply chain disruptions. Calculate the safety stock level based on factors like demand variability, lead time variability, and desired service level.
Below is an in-depth analysis of each step that will help you calculate minimum or maximum inventory levels. Let’s see how they work.
Gathering Essential Inventory Data
The first step in calculating min/max inventory levels is to gather essential inventory data. This data includes historical sales data, lead times, and safety stock requirements. It provides valuable insights into your inventory patterns and helps you make informed decisions.
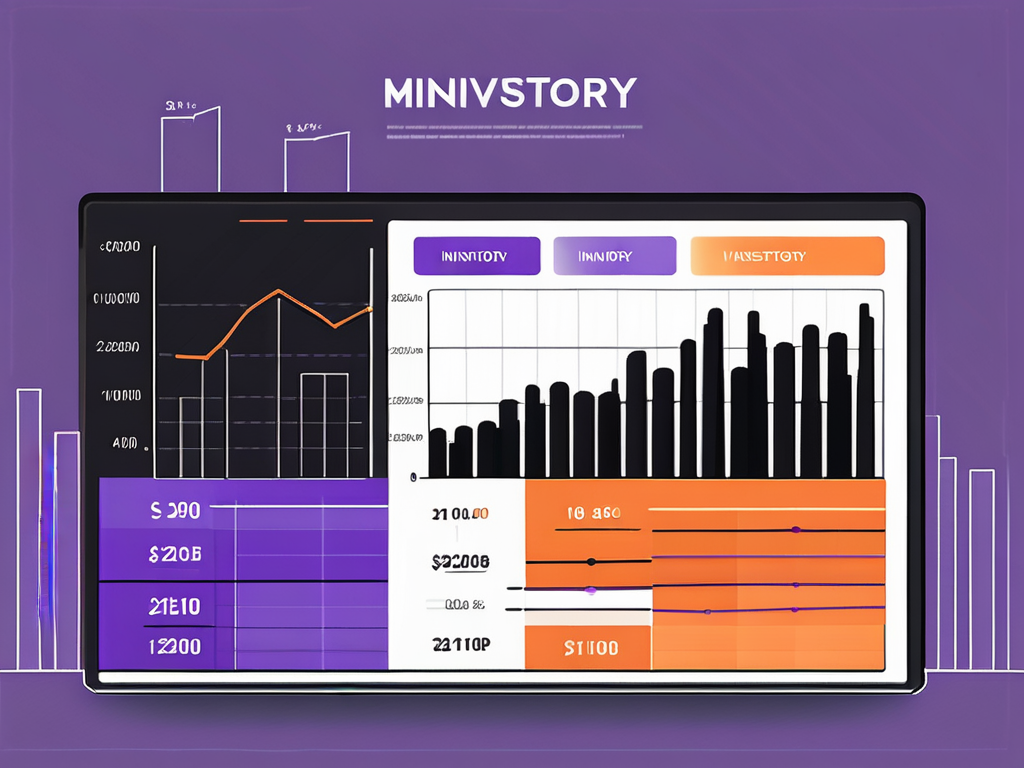
To gather this data, start by analyzing your sales history over a specific period. Look for any seasonal trends, high-demand periods, or slow-moving items. This information will guide your min/max calculations and ensure that you have the right stock levels to meet customer demand.
Additionally, consider collecting data on supplier performance, such as lead times and order fill rates. This information will help you assess the reliability of your suppliers and factor it into your inventory calculations.
Analyzing Inventory Turnover Rate
Knowing your inventory turnover rate is crucial in determining the optimal stock levels and replenishment frequency. This metric measures how quickly your inventory is used or sold within a specific period.
To calculate the inventory turnover rate, divide the cost of goods sold (COGS) by the average inventory value. The resulting ratio indicates how many times your inventory is bought and replaced in a given period.
Higher turnover rates often suggest that you can reduce your inventory while maintaining the desired service level. However, it’s important to consider industry benchmarks and customer expectations when analyzing your inventory turnover rate.
Some industries may require higher stock levels due to longer lead times or specific customer demands. Balancing inventory turnover with customer satisfaction is key to optimizing your inventory management.
Determining Safety Stock Levels
Safety stock acts as a buffer to address unforeseen fluctuations in demand or supply chain disruptions. It ensures that you can meet unexpected customer demands and avoid stockouts.
To determine safety stock levels, consider factors such as demand variability, lead time variability, and desired service level. Ideally, a higher level of demand variability or longer lead times would require a higher safety stock quantity to mitigate the associated risks.
Additionally, it’s important to regularly review and update your safety stock levels to adapt to changing market conditions and customer demands. As your business grows or faces new challenges, revisiting your safety stock calculations will help you maintain optimal inventory levels and customer satisfaction.
Implementing Min/Max Inventory System
Now that you’ve calculated your min/max inventory levels, it’s time to implement them effectively. Adopting a well-structured min/max inventory system will allow you to maintain optimal stock levels consistently.
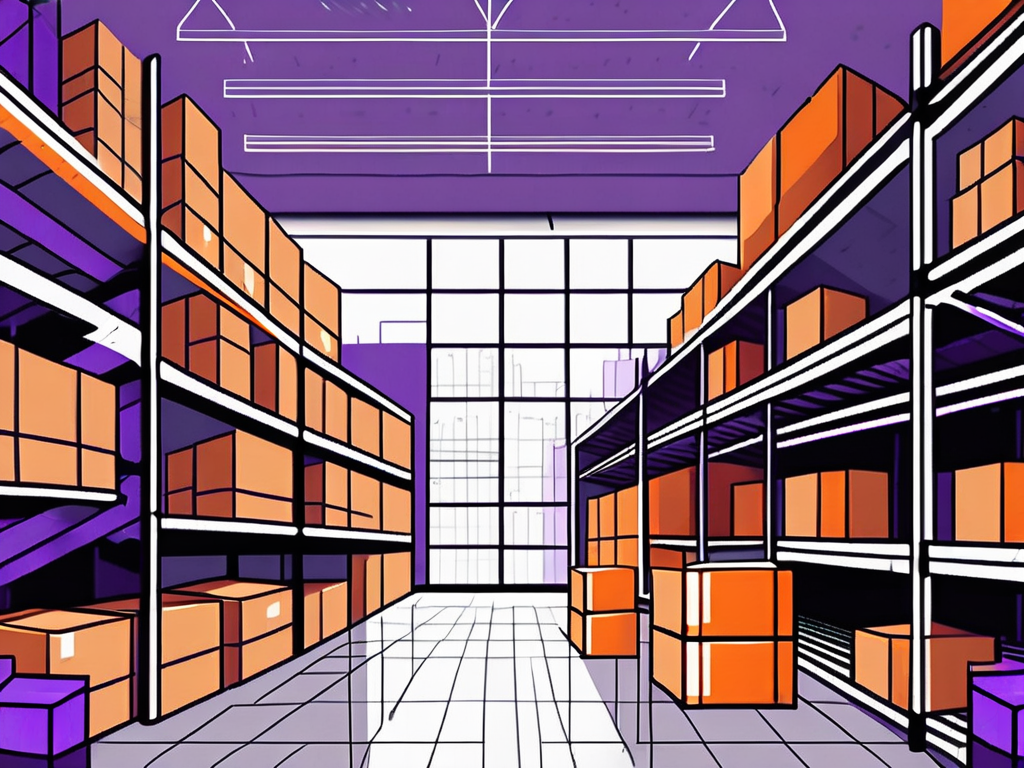
Having a robust min/max inventory system in place is crucial for businesses of all sizes. Not only does it help in preventing stockouts and overstock situations, but it also enhances operational efficiency and customer satisfaction.
By setting clear thresholds for minimum and maximum inventory levels, you create a systematic approach to inventory management that can lead to cost savings and improved cash flow.
Setting Up Your Min/Max Inventory System
To set up your min/max inventory system, ensure that you have reliable inventory management software or tools that enable accurate tracking of stock levels.
Implement automated reorder notifications based on your calculated minimum levels to streamline the procurement process and maintain smooth operations.
Additionally, consider integrating demand forecasting techniques into your inventory system to anticipate fluctuations in customer demand.
By leveraging historical sales data, market trends, and seasonality patterns, you can make informed decisions about adjusting your min/max levels to align with changing market conditions.
Moreover, establish clear procedures for updating and adjusting your min/max levels periodically. Regularly review demand patterns, supplier performance, and market dynamics to ensure that your inventory levels stay aligned with changing business needs.
Regularly Reviewing and Adjusting Levels
Effective inventory management is an ongoing process that requires continuous monitoring and fine-tuning. Regularly review and adjust your min/max levels based on real-time data to ensure the highest level of efficiency and profitability.
Stay proactive by staying updated on industry trends, identifying potential risks, and exploring opportunities for improvement. By doing so, you can adapt your min/max inventory levels accordingly, ensuring inventory control and sustained business success.
Benefits of Min/Max Inventory Management
Implementing an efficient min/max inventory management system offers several benefits that can positively impact your business operations and profitability.
One additional advantage of utilizing a min/max inventory management system is the ability to streamline procurement processes. By accurately determining the minimum and maximum levels of inventory required, businesses can establish more precise reorder points.
This leads to a reduction in the time and effort spent on manual inventory checks and order placements, allowing staff to focus on more strategic tasks that drive business growth.
Improved Inventory Control
By setting accurate min/max levels, businesses gain better control over their inventory. Optimal stock levels prevent stockouts, minimize carrying costs, and maximize order fulfillment rates, leading to improved customer satisfaction and organizational efficiency.
Furthermore, implementing a min/max inventory system can also enhance demand forecasting accuracy. By analyzing historical data and consumption patterns, businesses can make informed decisions about inventory levels.
This proactive approach enables companies to anticipate fluctuations in demand, adjust their min/max levels accordingly, and avoid overstocking or understocking situations.
Enhanced Cash Flow Management
A well-implemented min/max inventory system helps businesses optimize their cash flow management. By maintaining the right balance between inventory levels and customer demand, you can allocate working capital more efficiently and reduce the risk of excess inventory or stockouts.
In addition to improving cash flow management, a min/max inventory system can also contribute to better supplier relationships. By having a clear understanding of inventory needs and ordering patterns, businesses can negotiate more favorable terms with suppliers.
This can lead to cost savings, improved delivery schedules, and increased overall efficiency in the supply chain.
Potential Challenges in Min/Max Inventory Management
While min/max inventory management brings numerous benefits, it’s essential to be aware of potential challenges that businesses may encounter in the process. Here’s our top 4:
- Lead times refer to the time taken from placing an order to receiving the inventory. Longer lead times require more accurate predictions of future demand. Businesses need to factor in lead times when setting min/max levels to avoid stockouts or overstock situations.
- Failure to accurately calculate and maintain min/max inventory levels can lead to overstock or stockout scenarios. Overstocking ties up working capital and increases carrying costs. Stockouts result in missed sales and dissatisfied customers. Regular monitoring and adjustment of min/max levels can help mitigate these risks.
- Businesses must accurately manage seasonal demands and adjust their min/max levels to cater to increased or decreased demand during specific times of the year. Adopting sophisticated demand forecasting techniques and close monitoring of market trends can address this challenge effectively.
- Technology can streamline processes, improve accuracy, and provide real-time data insights. However, it requires initial investment, training, and maintenance. Businesses need to carefully assess their technological needs and capabilities to leverage the benefits of automation in inventory management.
Mastering Min/Max Inventory: The Key to Efficiency
In conclusion, accurate min/max inventory levels are essential for a well-functioning inventory management system. By understanding and calculating these levels effectively, businesses can optimize their stock levels and improve overall operational efficiency.