Did you know that determining the right size of a warehouse plays a crucial role in the success of a business?
Whether you’re a small startup or an established company, having the right amount of space is essential for efficient operations and customer satisfaction.
In this blog post, we will talk about:
- How to evaluate business demands for warehouse sizing
- The role of inventory in warehouse sizing
- Ways of calculating warehouse space requirements
- The impact of warehouse layout on space needs
Table of Contents
Toggle3 Questions You Need to Answer to Determine the Right Warehouse Size
To determine the warehouse size your business needs start by evaluating your current operations and future growth projections. Ask yourself questions these questions:
- What is the nature of your business? Are you dealing with perishable goods, bulky items, or fragile products that require special storage conditions?
- What is your current order volume? How many orders do you receive on a daily, weekly, or monthly basis?
- Do you plan to expand your product offerings in the future?
Considering these factors will help you get a clear picture of your warehouse needs and enable you to make informed decisions regarding its size.
Furthermore, it’s crucial to assess your inventory turnover rate. Understanding how quickly your products move in and out of the warehouse can impact the layout and design of your storage space. High turnover rates may require more efficient picking and packing areas, while slower-moving items may benefit from specialized storage solutions.
Another aspect to consider is the geographical location of your warehouse. Proximity to suppliers, customers, and transportation hubs can significantly impact your operational costs and delivery times.
For example, a centrally located warehouse may reduce shipping expenses and lead to faster order fulfillment, ultimately enhancing customer satisfaction.
Calculating Warehouse Space Requirements
Now that you have a clear understanding of your business requirements and inventory changes, it’s time to dive into the calculations.
Calculating warehouse space requirements involves considering various aspects, such as warehouse space utilization and specific tools and techniques.
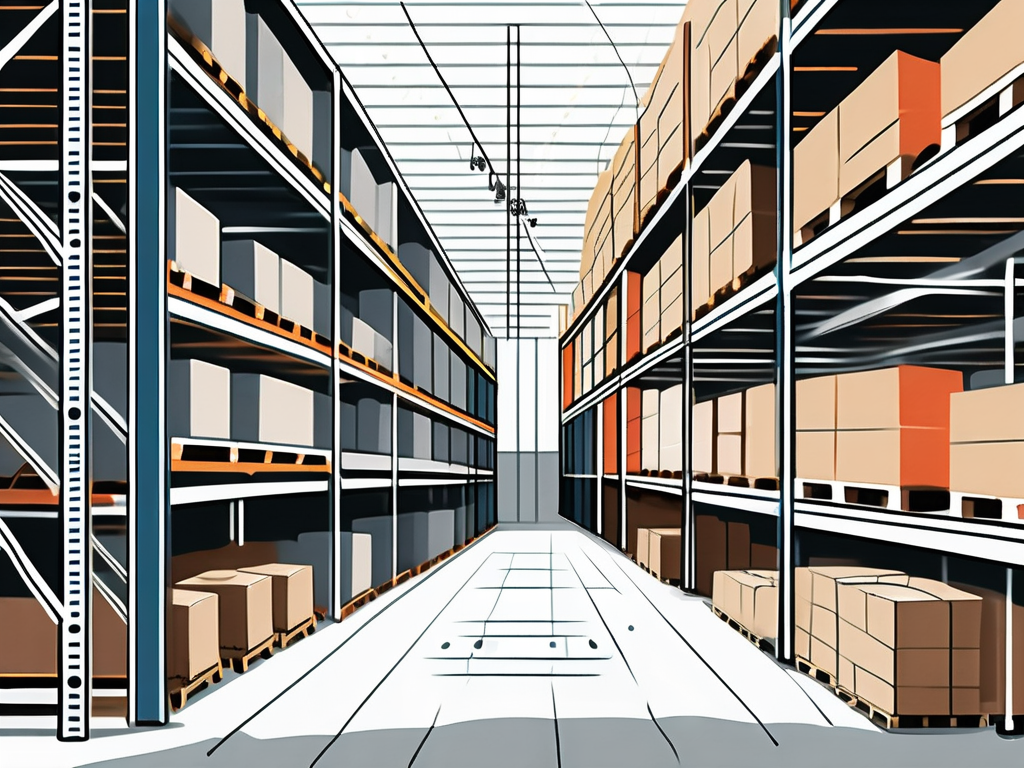
Understanding Warehouse Space Utilization
Warehouse space utilization refers to the efficient use of the available space. Maximizing utilization ensures optimal storage capacity and smooth operations.
Consider factors like the type of racking system, aisle width, and the height of the racks. Implementing efficient storage systems and layouts can significantly reduce wasted space and improve productivity.
For example, using narrow aisle racking systems can help you make the most of your vertical space. These systems allow for narrower aisles between racks, which means more racks can be installed in the same area. Additionally, utilizing mezzanine floors can create additional storage space without expanding the warehouse’s footprint.
Tools and Techniques for Space Calculation
To determine the size of a warehouse needed, you can utilize various tools and techniques. Some commonly used methods include:
- Space utilization software: Use software tools specifically designed to calculate warehouse space requirements based on your inventory data and storage systems. These tools take into account factors like product dimensions, turnover rates, and storage density to provide accurate space calculations.
- Manual measurements: Measure the dimensions of your products and calculate the required storage space based on their size and quantity. This method is particularly useful when dealing with irregularly shaped items or unique inventory.
- Expert consultation: Seek advice from warehouse consultants who specialize in space planning and optimization. These professionals can assess your specific business needs and recommend the most efficient warehouse size and layout.
Combining these tools and techniques will help you arrive at accurate calculations and make informed decisions regarding your warehouse size. Remember, it’s crucial to regularly reviewand reassess your space requirements as your business evolves and grows.
By continuously optimizing your warehouse space utilization and staying up-to-date with the latest tools and techniques, you can ensure that your warehouse operates at maximum efficiency, ultimately leading to improved profitability and customer satisfaction.
The Impact of Warehouse Layout on Space Needs
Warehouse layout plays a critical role in determining space needs. A well-designed and optimized layout can significantly reduce space requirements while improving efficiency and productivity. Let’s explore some key factors that influence warehouse layout.
When considering warehouse layout, it’s essential to take into account the type of products being stored. Different products have varying storage requirements, such as temperature control, shelf life, and fragility.
By understanding these needs, you can tailor the layout to maximize space utilization while ensuring the safety and integrity of the stored items.
Optimizing Warehouse Design for Space Efficiency
An optimized warehouse design focuses on reducing unnecessary movements and streamlining operations. Consider factors like product flow, layout organization, and logical placement of different areas such as receiving, storage, and shipping. By optimizing your layout, you can make the most of your available space and minimize the need for additional square footage.
Another crucial aspect of warehouse layout is the incorporation of technology and automation. Implementing technologies such as warehouse management systems can enhance space utilization and operational efficiency. These tools can help in real-time inventory tracking, order fulfillment, and space optimization, ultimately reducing the overall space requirements of the warehouse.
The Role of Aisle Width and Rack Height
Aisle width and rack height directly impact storage capacity and overall space requirements. Narrower aisles and higher racks allow for increased vertical space utilization.
However, it’s important to strike a balance between space optimization and operational efficiency. Ensure that you consider factors like accessibility, safety regulations, and equipment maneuverability when determining aisle width and rack height.
In addition to aisle width and rack height, the layout should also account for future scalability and flexibility. As businesses evolve and product lines expand, the warehouse layout should be adaptable to accommodate growth.
Incorporating modular storage systems and flexible racking solutions can help in adjusting to changing space needs without requiring a complete overhaul of the layout.
Other Factors Influencing Warehouse Size
In addition to the factors discussed above, there are other considerations that can influence the size of the warehouse needed.
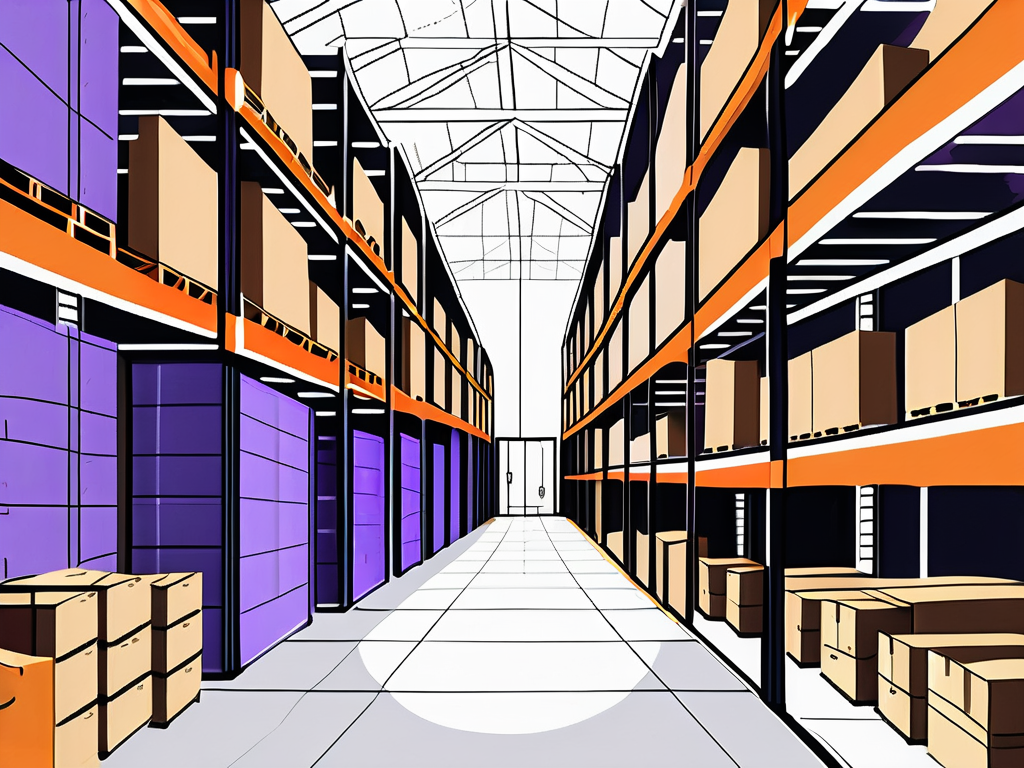
Considering Staff and Equipment Space
When determining the size of your warehouse, it’s essential to allocate space not only for storing your inventory but also for staff workstations, break areas, restrooms, and equipment storage. Neglecting these areas can lead to cramped and inefficient working conditions.
Additionally, it’s crucial to plan for future staff expansion as your business grows. Having enough space for your employees to move comfortably and efficiently will contribute to a smooth workflow and promote a positive work environment.
The Importance of Safety and Compliance in Warehouse Sizing
While evaluating the size of your warehouse, it is imperative to consider safety regulations and compliance requirements. Adequate space must be allocated for fire exits, emergency equipment, and storage of hazardous materials, if applicable.
Failing to meet these requirements can have severe consequences, including potential accidents, legal issues, and damage to your reputation. It’s crucial to ensure that your warehouse adheres to all safety standards to protect your employees and the integrity of your products.
Moreover, compliance with industry-specific regulations is equally important. Depending on the nature of your business, you may need to consider additional space for specialized equipment, such as temperature-controlled storage for perishable goods or secure areas for handling sensitive information.
By incorporating these considerations into your warehouse sizing decisions, you can ensure that your operations remain in line with industry standards and avoid any potential setbacks.
Enhance Your Warehousing with Our Sizing Tips
Determining the size of a warehouse needed is a critical decision that requires careful evaluation of various factors. By understanding your business requirements, you can make informed decisions that will contribute to the success of your business.
Remember, choosing an efficiently sized warehouse is key to maintaining smooth operations, satisfying customer demands, and ultimately achieving your business goals.