Shipping delays can be a major challenge for businesses of all sizes. They can lead to frustrated customers, lost sales, and damage to a company’s reputation. However, with the right strategies and approaches, it is possible to handle shipping delays effectively and minimize their impact on your business.
In this article, we will explore:
- The causes of shipping delays
- The importance of communication during delays
- Strategies to mitigate delays
- Developing contingency plans
- Evaluating the impact of delays on your business
Table of Contents
Toggle3 Effective Strategies for Handling Shipping Delays
Shipping delays can significantly impact a company’s bottom line and customer satisfaction. Implementing effective strategies to mitigate these delays is crucial for maintaining a competitive edge in today’s fast-paced market.
Here are some key strategies businesses can adopt to minimize the impact of shipping delays.
Strategy 1: Enhancing Supply Chain Management
Efficient supply chain management is crucial for timely deliveries. Streamlining processes, optimizing inventory levels, and establishing strong relationships with reliable logistics partners can help reduce the risk of delays.
Investing in technologies such as warehouse management systems or transportation management software can improve visibility and control over the supply chain, enabling quick responses to potential disruptions.
- Streamline Processes: Implement efficient workflows and reduce unnecessary steps.
- Optimize Inventory Levels: Maintain optimal stock levels to avoid shortages or overstock.
- Establish Strong Relationships: Partner with reliable logistics providers for better service.
- Invest in Technology: Use warehouse and transportation management systems for better visibility.
Moreover, fostering collaboration and communication among all stakeholders in the supply chain is essential. By sharing real-time data and insights, businesses can proactively address issues and work together to find solutions, ultimately minimizing the impact of delays on overall operations.
Strategy 2: Leveraging Technology for Improved Efficiency
Technological advancements have revolutionized the shipping industry. Companies can leverage automation, artificial intelligence, and data analytics to enhance operational efficiency and identify potential bottlenecks before they lead to delays.
Automated tracking systems, real-time visibility of shipments, and predictive analytics can empower businesses with valuable insights and enable proactive decision-making.
- Automation: Implement automated systems for inventory tracking and order processing.
- Artificial Intelligence: Use AI to predict and manage potential delays.
- Data Analytics: Analyze shipping data to identify and address bottlenecks.
- Real-Time Tracking: Provide real-time visibility of shipments to improve transparency.
Furthermore, embracing sustainability practices in shipping operations can also contribute to reducing delays. Implementing eco-friendly packaging materials, optimizing transportation routes to minimize carbon emissions, and partnering with environmentally conscious carriers can help mitigate delays while demonstrating a commitment to environmental responsibility.
Strategy 3: Diversifying Shipping Methods and Carriers
Another effective strategy to mitigate shipping delays is diversifying shipping methods and carriers. Relying on a single carrier or shipping method can increase vulnerability to delays caused by unforeseen disruptions.
By using multiple carriers and a mix of shipping methods, businesses can create a more flexible and resilient logistics network.
- Multiple Carriers: Establish relationships with several carriers to have backup options.
- Mixed Shipping Methods: Use a combination of air, sea, and ground transportation.
- Alternative Routes: Plan for alternative routes to avoid potential disruptions.
- Capacity Issues: Ensure there are options if one provider faces capacity problems.
For instance, combining air, sea, and ground transportation options can provide alternative routes if one mode of transport is delayed. Additionally, establishing relationships with multiple carriers ensures that businesses have backup options in case of capacity issues or service interruptions with one provider.
This diversification helps maintain delivery schedules and reduces the risk of significant delays impacting the entire supply chain.
The Importance of Communication During Delays
Effective communication is key when dealing with shipping delays. It helps:
- Manage customer expectations
- Maintain transparency with business partners
- Build trust
Timely and accurate information about delays can go a long way in ensuring customer satisfaction and loyalty.
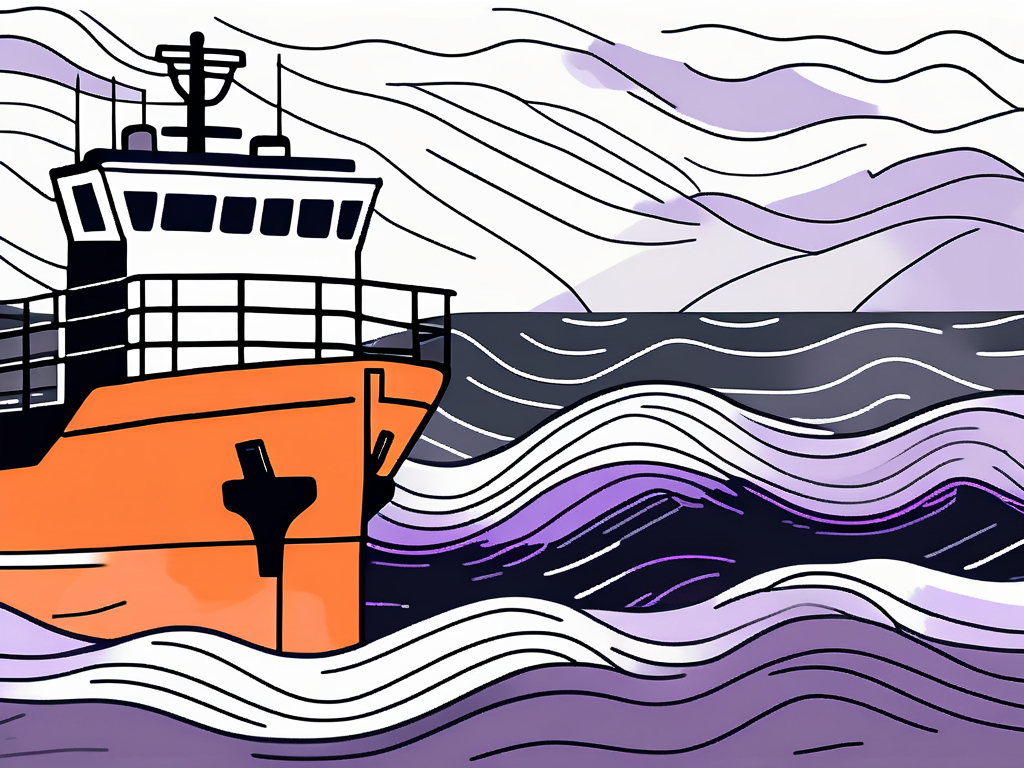
Furthermore, communication during delays is not just about conveying the problem at hand but also about showcasing your commitment to resolving issues efficiently. By demonstrating a proactive approach and offering solutions or compensation where appropriate, businesses can turn a potentially negative situation into a positive customer experience.
Keeping Customers Informed
When a shipping delay occurs, it is essential to provide prompt updates to customers. This can be done through various channels such as email, SMS notifications, or tracking systems. Clear and concise communication about the delay, expected delivery time, and any additional steps being taken to resolve the situation can help alleviate customer concerns and maintain their trust in your business.
In addition to providing updates, businesses can also use delays as an opportunity to engage with customers. Offering personalized messages, discounts on future purchases, or even small gestures like handwritten notes can show customers that their satisfaction is a top priority, fostering long-term loyalty.
Transparency with Business Partners
Shipping delays not only affect your customers but can also impact your relationships with business partners. By communicating proactively with your suppliers, retailers, or distributors, you can minimize disruptions to their operations and collaborate on alternative solutions to fulfill orders. Transparent communication builds stronger partnerships and ensures smooth business operations even in challenging situations.
Moreover, maintaining open lines of communication with business partners during delays can lead to valuable insights and improvements in supply chain management. By sharing data on delays, identifying root causes, and collectively brainstorming preventive measures, companies can strengthen their collaborative efforts and enhance overall operational efficiency.
Developing a Contingency Plan for Unexpected Delays
Despite meticulous planning, unexpected delays may still occur. Having a well-defined contingency plan in place can help businesses respond effectively to such situations and minimize disruptions.
One key aspect of developing a contingency plan for unexpected delays is to ensure clear communication channels both internally and externally. Internally, all team members should be aware of the procedures to follow in case of a delay, including who to contact and how to rearrange priorities.
Externally, customers and partners should be kept informed of any potential delays and the steps being taken to mitigate them, fostering transparency and trust.
Risk Assessment and Management
Conducting a comprehensive risk assessment allows businesses to identify potential threats in the supply chain and develop strategies to mitigate them. This could involve:
- Diversifying transportation routes
- Establishing multiple sourcing options
- Securing alternative warehousing facilities
By proactively addressing risks, businesses can better navigate unexpected delays and maintain continuity in their operations. Moreover, collaborating with key stakeholders such as suppliers, logistics partners, and regulatory bodies can enhance the effectiveness of risk management efforts.
Building a Resilient Business Model
Building resilience is crucial to handling shipping delays effectively. This involves developing a flexible business model that can adapt to changing circumstances. By fostering agility, businesses can quickly adjust their operations, explore alternative shipping methods, or prioritize critical orders during delays, minimizing the impact on customers and their bottom line.
Furthermore, investing in technology solutions such as real-time tracking systems, predictive analytics, and inventory management software can significantly enhance a company’s ability to respond to unexpected delays. These tools provide valuable data insights, improve decision-making processes, and enable proactive measures to mitigate risks before they escalate into major disruptions.
Evaluating the Impact of Shipping Delays on Business
Shipping delays have far-reaching consequences for businesses. Understanding the impact of these delays allows businesses to make informed decisions and implement necessary measures to mitigate potential losses.
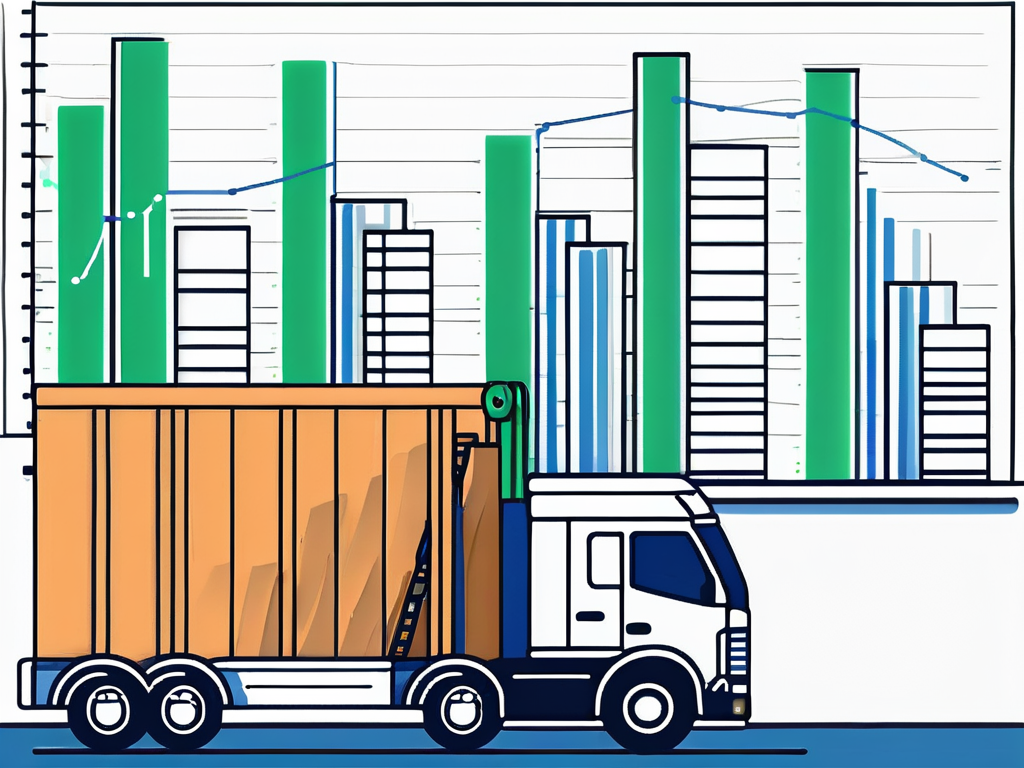
Customer Satisfaction and Retention
Shipping delays can lead to dissatisfied customers who may take their business elsewhere. This can have a significant impact on customer satisfaction and retention rates. Customers expect timely delivery of their orders, and any delays can result in frustration and disappointment. To address this, businesses need to prioritize effective communication with customers.
Providing regular updates on the status of their orders and offering solutions, such as expedited shipping or discounts on future purchases, can help alleviate customer concerns and retain their loyalty.
Additionally, monitoring customer feedback, addressing concerns promptly, and implementing improvement measures based on customer insights can enhance customer satisfaction even during challenging times.
Financial Implications of Shipping Delays
Shipping delays can result in additional costs for businesses, such as expedited shipping fees or inventory holding expenses. These financial implications can put a strain on a business’s resources and profitability.
To mitigate these losses, businesses need to evaluate the financial impact of shipping delays. By analyzing the costs associated with delays, businesses can implement cost-effective measures, negotiate favorable terms with shipping providers, and optimize their financial resources.
Expanding on the topic of shipping delays, it is important to consider the potential reputational damage that can occur. In today’s interconnected world, news of shipping delays can spread quickly through social media and online platforms, potentially tarnishing a business’s reputation. Negative reviews and comments about delayed shipments can discourage potential customers from engaging with the business, leading to a loss of sales and opportunities.
Therefore, businesses must not only focus on addressing the immediate impact of shipping delays but also invest in building a strong reputation and brand image.
Causes of Shipping Delays
Shipping delays can arise from various factors. One of the main causes is weather conditions. Extreme weather events such as hurricanes, snowstorms, or heavy rainfall can disrupt transportation routes and lead to delays in the delivery process. Global events also play a significant role in shipping delays. Political unrest, natural disasters, or pandemics can impact the operations of shipping companies and result in longer delivery times.
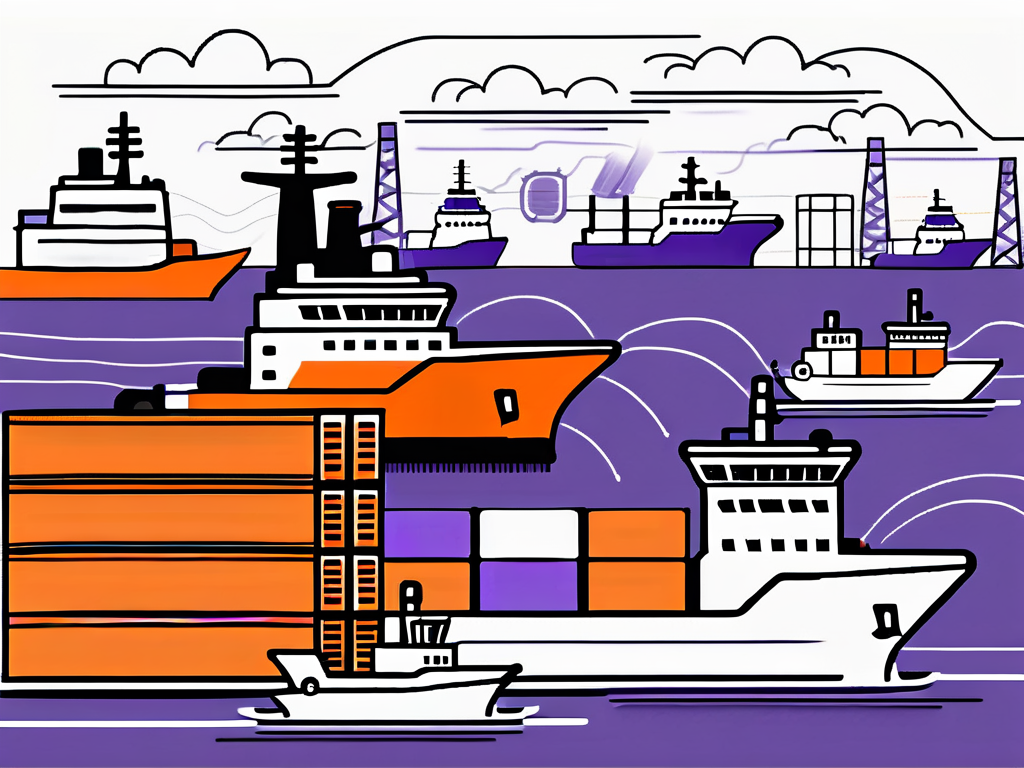
The Role of Weather Conditions in Shipping Delays
Weather conditions can have a significant impact on shipping delays. Severe storms, heavy winds or icy road conditions can make it unsafe for transportation vehicles to operate, leading to delays in the delivery process. Shipping companies must closely monitor weather forecasts and take appropriate measures to ensure the safety of their employees and goods in transit.
For example, during the winter season, snowstorms can create hazardous road conditions, making it difficult for trucks to navigate through slippery roads. In such cases, shipping companies may need to reroute their vehicles or temporarily halt operations until the weather conditions improve. These precautions are necessary to avoid accidents, protect the integrity of the goods, and ensure the well-being of the employees.
Impact of Global Events on Shipping Times
Global events such as political instability, trade disputes, or health crises can have a profound impact on shipping times. For instance, during a pandemic, travel restrictions and lockdown measures can disrupt supply chains and cause delays in the transportation of goods. It is crucial for businesses to stay informed about global events and have contingency plans in place to navigate these challenges.
During times of political unrest, shipping companies may face difficulties in accessing certain regions or ports due to security concerns. This can lead to delays as alternative routes need to be identified and additional security measures need to be implemented. Similarly, trade disputes between countries can result in increased customs inspections and paperwork, causing delays in the clearance process at ports of entry.
Operational Challenges Leading to Delays
Inefficient logistics systems, understaffed warehouses, or technical malfunctions can also contribute to shipping delays. It is important for businesses to constantly evaluate their operations and identify areas for improvement.
By investing in enhanced supply chain management and adopting advanced technologies, companies can streamline their processes and reduce the risk of delays.
For example, implementing automated inventory management systems can help businesses accurately track and manage their stock levels, reducing the chances of delays caused by stockouts or inventory discrepancies. Additionally, optimizing warehouse layouts and staffing levels can improve efficiency and minimize the time required for order fulfillment.
With the Right Approach, You Can Handle Delays as Efficiently as Possible
Handling shipping delays effectively requires a proactive approach, effective communication, and strategic planning. By understanding the causes of delays, implementing mitigation strategies, and evaluating the impact on your business, you can navigate through shipping challenges and ensure customer satisfaction. Remember, while delays may be unavoidable at times, your response to those delays can make all the difference in maintaining a thriving business.