According to a study conducted by the Institute of Supply Management, 60% of order picking operations’ total warehouse costs are spent on labor.
With such a significant investment, it is crucial for companies to measure and optimize their picking productivity. But what exactly is picking productivity, and how do you measure it? In this article, we’ll explore:
- Main KPIs for picking productivity measurements
- Eessential tools for tracking and managing productivity
- Strategies to improve picking productivity
- Importance of analyzing and interpreting productivity data
Table of Contents
ToggleTop 3 KPIs for Measuring Picking Productivity
When it comes to measuring picking productivity, several key metrics can provide valuable insights into your operations.
Efficient picking processes are crucial for the smooth operation of any warehouse or distribution center. By analyzing key metrics, you can gain a deeper understanding of your workforce’s performance and make informed decisions to enhance productivity.
1. Pick Rate
The pick rate measures the number of items picked per hour or per shift. It helps you understand how quickly your workforce is retrieving items from the warehouse shelves. Monitoring the pick rate allows you to identify opportunities for improvement, such as rearranging product placement or optimizing pick paths.
Additionally, a high pick rate not only indicates efficiency but also reflects the effectiveness of your inventory management system. By maintaining a consistent and high pick rate, you can ensure timely order fulfillment and customer satisfaction.
2. Order Accuracy
Order accuracy measures the percentage of orders picked correctly without any errors. It is essential to ensure customer satisfaction and reduce the costs associated with returns and re-shipping. Tracking order accuracy allows you to identify areas where additional training or process adjustments are needed.
Furthermore, maintaining a high level of order accuracy is crucial for building customer trust and loyalty. By consistently delivering orders correctly, you can establish a reputation for reliability and quality service in the competitive market.
3. Utilization Rate
The utilization rate measures the percentage of time your workforce spends on value-added picking activities compared to non-value-added activities, such as walking or waiting. By tracking the utilization rate, you can identify inefficiencies in your processes and allocate resources more effectively.
Optimizing the utilization rate not only improves productivity but also enhances employee satisfaction. By minimizing non-value-added activities and maximizing time spent on productive tasks, you can create a more engaging work environment and boost overall morale within your workforce.
Tools for Measuring Picking Productivity
There are several tools with which you can manage picking productivity. Let’s explore them one by one.
Warehouse Management Systems
Warehouse management systems (WMS) are software applications that help companies manage their warehouse operations efficiently. They provide real-time visibility into inventory levels, enable efficient order fulfillment, and capture data for reporting and analysis. A WMS can generate accurate picking productivity metrics based on actual picking activities.
Furthermore, WMS can optimize warehouse layout and storage strategies, leading to reduced travel time for pickers and increased overall efficiency. By utilizing advanced algorithms, WMS can suggest the most efficient picking routes and methods, ultimately enhancing productivity and reducing operational costs.
Labor Management Systems
Labor management systems (LMS) focus specifically on optimizing workforce productivity. They track labor performance metrics, such as pick rates and order accuracy, in real-time. By providing visibility into individual and team performance, an LMS helps identify coaching opportunities and enables performance-based incentives.
In addition, LMS can integrate with other systems like payroll and scheduling software to streamline workforce management processes. By analyzing historical data and trends, LMS can forecast labor requirements accurately, ensuring that the right number of workers are available during peak picking times to maintain high productivity levels.
Strategies to Improve Picking Productivity
Implementing Efficient Picking Methods
Implementing efficient picking methods, such as batch picking or zone picking, can significantly improve productivity. Batch picking involves picking multiple orders simultaneously, while zone picking assigns pickers specific areas or zones within the warehouse. These methods reduce travel time and enable more efficient use of labor resources.
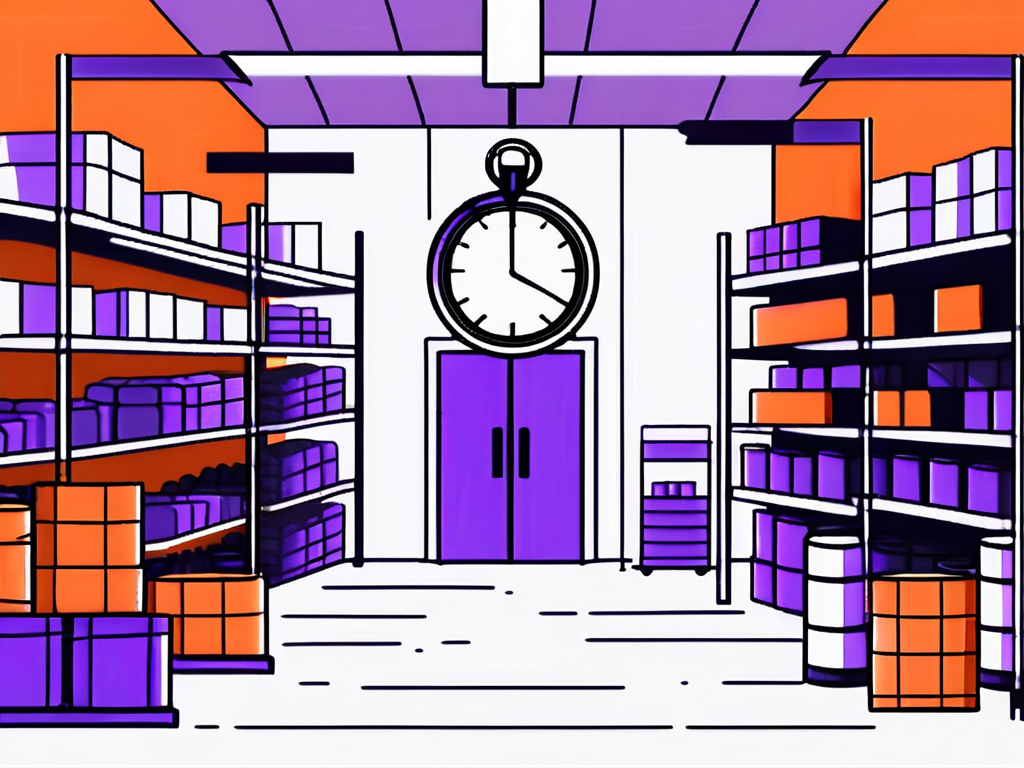
Another effective method to optimize picking productivity is wave picking. Wave picking involves grouping orders into waves and releasing them at specific intervals. This method optimizes the picking process by consolidating similar orders and reducing the time spent traveling between different locations in the warehouse.
Training and Motivating Staff
Investing in comprehensive training programs and creating a positive work environment can greatly impact picking productivity. A well-trained workforce understands the importance of accuracy and efficiency, while motivated employees take pride in their work and strive for excellence. Providing ongoing training and recognition opportunities can enhance employee engagement and productivity levels.
Furthermore, implementing a performance-based incentive system can further motivate staff to improve picking productivity. By rewarding employees based on their picking accuracy and speed, companies can create a culture of healthy competition and drive continuous improvement in the warehouse operations.
Analyzing and Interpreting Picking Productivity Data
Regularly analyzing picking productivity data allows you to identify trends and patterns that can impact performance. For example, you might notice that certain items are frequently out of stock, leading to inefficient picking processes. By understanding these patterns, you can take proactive measures to improve availability, optimize shelf locations, or adjust staffing levels.
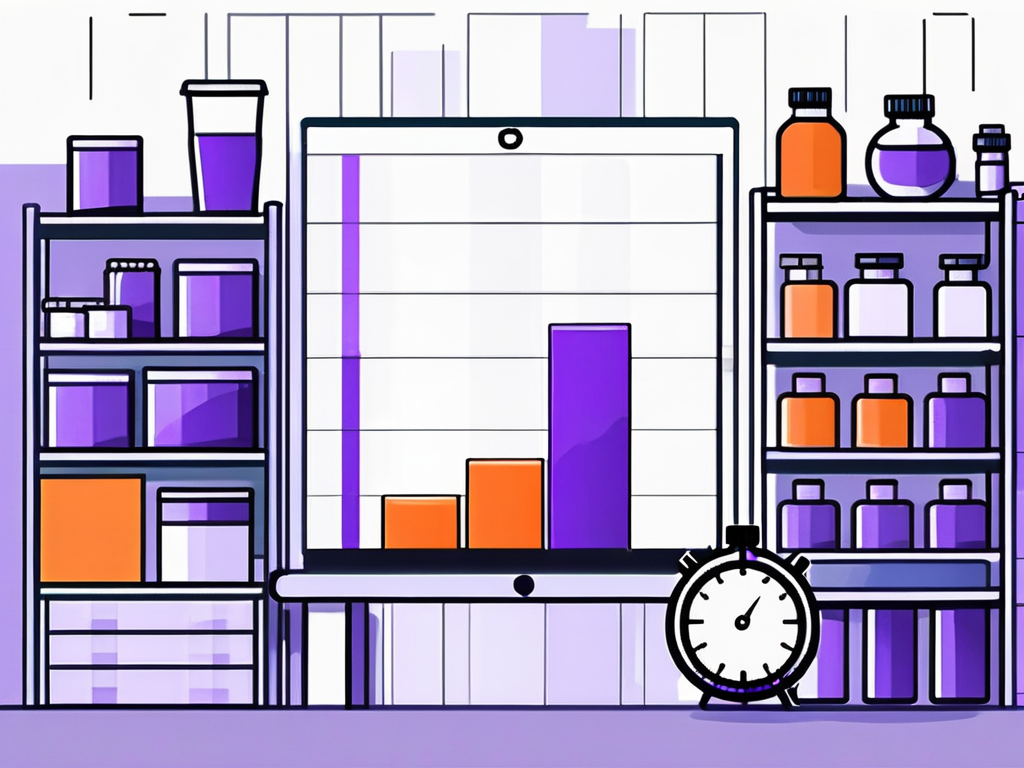
Moreover, delving deeper into the data may reveal seasonal trends or fluctuations in demand for specific products. Understanding these patterns can help you anticipate peak periods and allocate resources more effectively. By analyzing historical data alongside real-time information, you can fine-tune your operations to meet customer demands efficiently.
Making Informed Decisions for Improvement
Armed with accurate picking productivity data, you can make informed decisions to improve your operations. Whether it’s investing in automation technologies, optimizing warehouse layouts, or refining standard operating procedures, data-driven insights enable you to identify areas of improvement and implement targeted strategies for enhanced productivity.
Furthermore, by benchmarking your picking productivity against industry standards or competitors, you can gain valuable insights into where your operations stand. This comparative analysis can highlight potential areas for growth or efficiency gains, guiding your decision-making process towards achieving operational excellence.
Enhance Warehouse Efficiency by Mastering Picking Productivity
Measuring picking productivity is crucial for optimizing warehouse operations and ensuring customer satisfaction. By understanding the key metrics, leveraging the right tools, implementing effective strategies, and analyzing data, companies can make informed decisions and continuously improve their picking processes.
Remember, it’s not only about how fast items are picked but also about accuracy, efficiency, and the overall experience you provide to your customers.